thedesigner75
Automotive
- Jan 6, 2023
- 16
Hello to everybody,
i have a complex plastic part...the strange "nose" you can see in the picture attached is used as locator (datum feature B): to qualify this datum feature i have the size dimension on B but how can i check the orientation to A? It is a complex and irregular feature without any axis to be used for orientation...then i thought to put a tangent plane in one point of the feature putting a tolerance for the angle to A...is it correct? thank you for your time and support, ciao
i have a complex plastic part...the strange "nose" you can see in the picture attached is used as locator (datum feature B): to qualify this datum feature i have the size dimension on B but how can i check the orientation to A? It is a complex and irregular feature without any axis to be used for orientation...then i thought to put a tangent plane in one point of the feature putting a tolerance for the angle to A...is it correct? thank you for your time and support, ciao
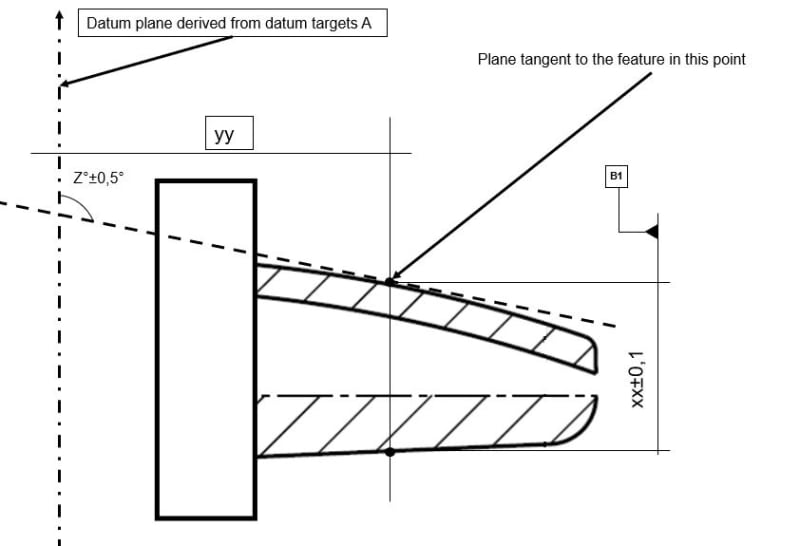