Good afternoon.
I'm trying to calculate the kW usage per hour for the following Ingersoll Rand Compressor. Does anyone know how I could find it based on the following plate stamped on the side? I know next to nothing on what these ratings even mean, I just have a strong suspicion our facility could be saving quite a bit of money if we shut them down daily when the facility is not running. If I can get their kW usage per hour I can easily run that against what DTE is charging us per kW. Even if it's not during peak time, I suspect those savings could add up.
Any help would be appreciated.
edit - grammar.
I'm trying to calculate the kW usage per hour for the following Ingersoll Rand Compressor. Does anyone know how I could find it based on the following plate stamped on the side? I know next to nothing on what these ratings even mean, I just have a strong suspicion our facility could be saving quite a bit of money if we shut them down daily when the facility is not running. If I can get their kW usage per hour I can easily run that against what DTE is charging us per kW. Even if it's not during peak time, I suspect those savings could add up.
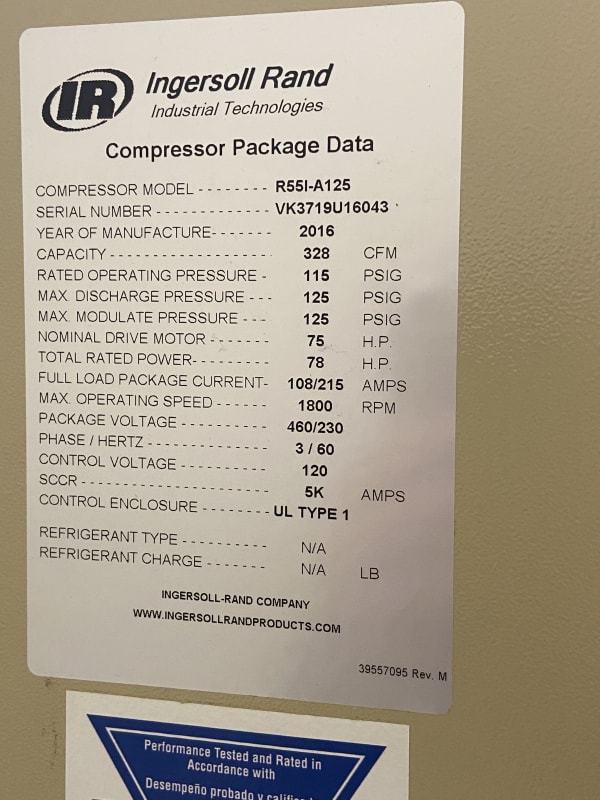
Any help would be appreciated.
edit - grammar.