Isaacwjp
Civil/Environmental
- Jun 13, 2023
- 4
Hi All,
I am currently doing a project at a site that uses ABB ACS880 VFD.
As you can see from the tracer below, the VFD Tripped at 43Hz due to the fault: Overspeed.
I am unable to identify the root cause.
-Shouldn't the fault only occur on 50Hz?
-Does the trip margin change based on the current Hz?
-For anyone using this model, do we have to set the trip margin manually?
Really need help identifying the root cause..
I am currently doing a project at a site that uses ABB ACS880 VFD.
As you can see from the tracer below, the VFD Tripped at 43Hz due to the fault: Overspeed.
I am unable to identify the root cause.
-Shouldn't the fault only occur on 50Hz?
-Does the trip margin change based on the current Hz?
-For anyone using this model, do we have to set the trip margin manually?
Really need help identifying the root cause..
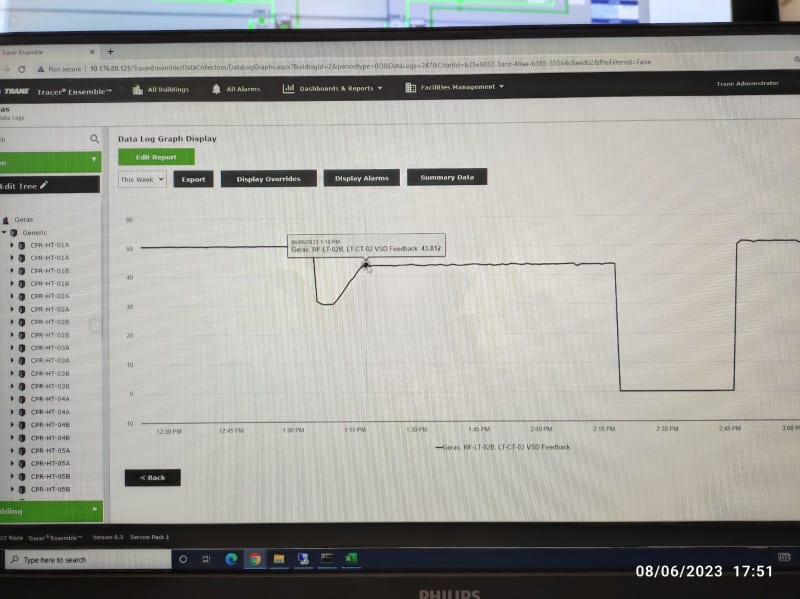
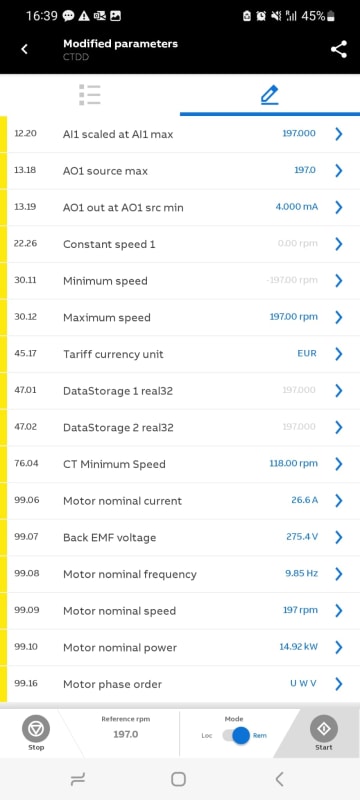
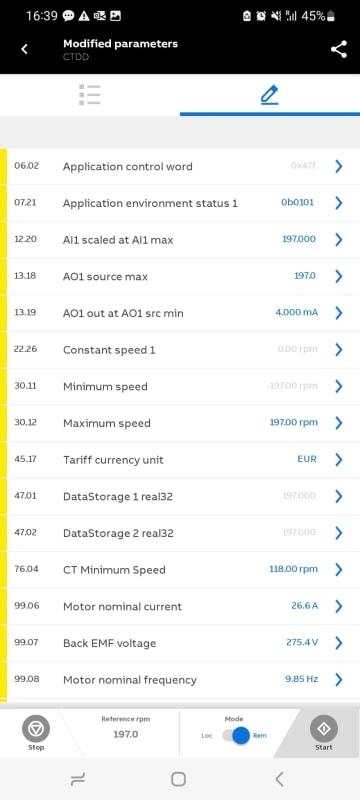
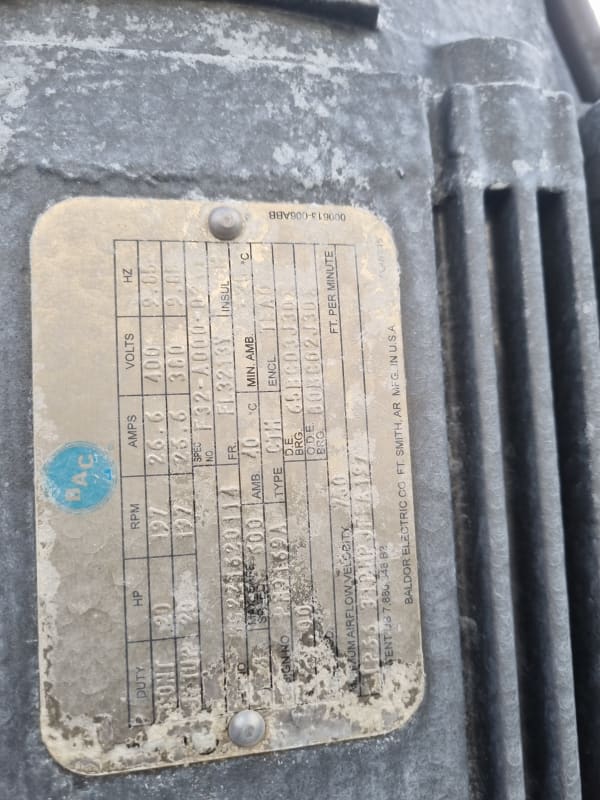
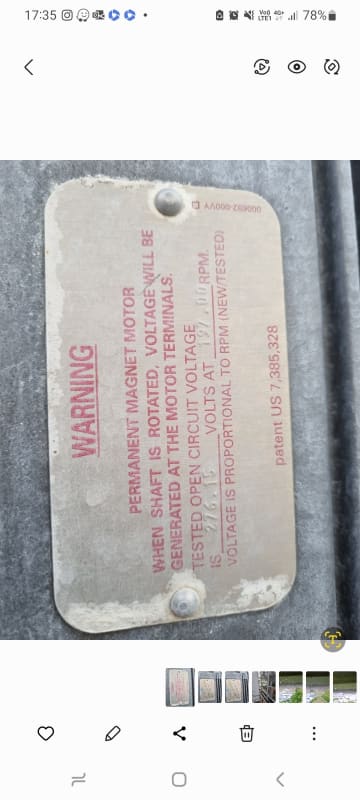