ShadowWarrior
Civil/Environmental
- Aug 21, 2006
- 171
In continuation of thread799-390004, I have the same geometry but with a vertical extension this time. I would appreciate community's help in achieving all Hexa mesh of this new part. The problem I'm facing is to partition it in appropriate regions to get all Hexa mesh.
This is the new part -
This is the mesh I got so far from the new part by following the previous partitioning scheme (green = structured = Hexa mesh). When trying to partition cell by defining cutting plane, the vertical part also get cut (see Red box). And its not possible to cut partition between the vertical part and the main cylinder (see black circle.
PS: the previous problem was solved by simply deleting surfaces from unwanted regions in ABAQUS.
This is the new part -
This is the mesh I got so far from the new part by following the previous partitioning scheme (green = structured = Hexa mesh). When trying to partition cell by defining cutting plane, the vertical part also get cut (see Red box). And its not possible to cut partition between the vertical part and the main cylinder (see black circle.
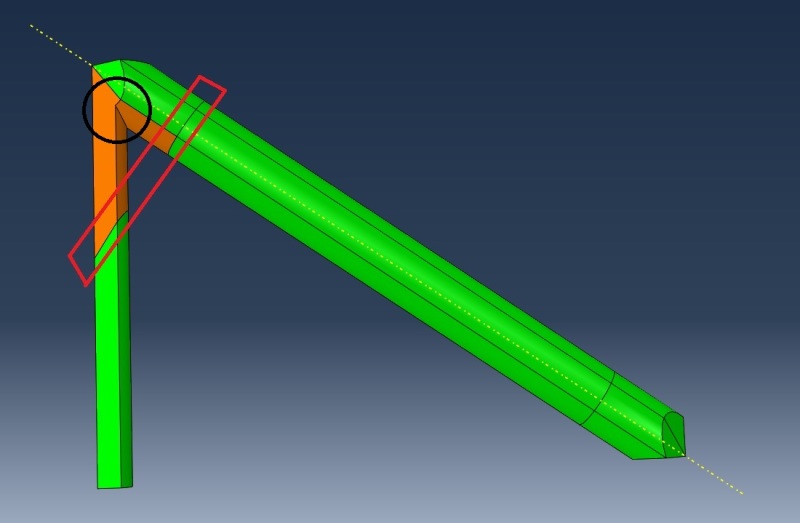
PS: the previous problem was solved by simply deleting surfaces from unwanted regions in ABAQUS.