Hello. I hope somebody will be able to help.
I have designed some equipment to assemble some large parts. It involves a stand and a fixture attached to it via a worm gear box.
The fixture and part needs to tip over at 90 degrees, from vertical to horizontal, and back.
After design and build, the specification has changed. I am not sure if the motor is going to be strong enough.
The total weight being lifted is 120kg.
The distance of mass from the pivot point is 280mm.
The current geared motor is 0.127 Nm. It is planetary geared to 100:1. Roughly I think this gives 12 Newton Meters.
The motor output Rpm is 60.
I have hooked this motor up to a 30:1 NMRV worm gear box, because 60rpm is too fast. I ideally wanted to rotate the fixture 90 degrees in less than 10 seconds, but no more than 20.
I have read that the calc for Final Torque is: Initial Motor Torque x Gear Ratio.
I have therefore taken the original motor torque and multiplied it by 130:1 total gearing. 0.127 x 130 = 16.5 Nm.
So far so good?.....
My weight is 120kg at 280mm from pivot. To get this back into meters, I have divided One Meter by 280mm, which gives 3.55. (Ie, 280mm fits 3.55 times into a meter).
120kg divided by 3.55 = approx 34kg at 1 meter. For certainty I am calling it 35kg.
So I have a mass of 35Kg at 1 meter from the pivot, which is then being worked back through a 30:1 worm gear box, then back to the 100:1 motor gearbox.
Is any of this right?
Can anybody help me understand what I now need to do with this 35kg, to know what the output torque of the motor needs to be, prior to the 30:1 gearbox?
Ie, taking the motor as it is now, at 12 Nm, or 16Nm through the second gearing, would this be enough to lift the weight?
Sorry if this is hard to understand, or something that is normally very simple for you guys. (Automation and motors etc are not usually my kind of work).
Many thanks
Sirius.
I have designed some equipment to assemble some large parts. It involves a stand and a fixture attached to it via a worm gear box.
The fixture and part needs to tip over at 90 degrees, from vertical to horizontal, and back.
After design and build, the specification has changed. I am not sure if the motor is going to be strong enough.
The total weight being lifted is 120kg.
The distance of mass from the pivot point is 280mm.
The current geared motor is 0.127 Nm. It is planetary geared to 100:1. Roughly I think this gives 12 Newton Meters.
The motor output Rpm is 60.
I have hooked this motor up to a 30:1 NMRV worm gear box, because 60rpm is too fast. I ideally wanted to rotate the fixture 90 degrees in less than 10 seconds, but no more than 20.
I have read that the calc for Final Torque is: Initial Motor Torque x Gear Ratio.
I have therefore taken the original motor torque and multiplied it by 130:1 total gearing. 0.127 x 130 = 16.5 Nm.
So far so good?.....
My weight is 120kg at 280mm from pivot. To get this back into meters, I have divided One Meter by 280mm, which gives 3.55. (Ie, 280mm fits 3.55 times into a meter).
120kg divided by 3.55 = approx 34kg at 1 meter. For certainty I am calling it 35kg.
So I have a mass of 35Kg at 1 meter from the pivot, which is then being worked back through a 30:1 worm gear box, then back to the 100:1 motor gearbox.
Is any of this right?
Can anybody help me understand what I now need to do with this 35kg, to know what the output torque of the motor needs to be, prior to the 30:1 gearbox?
Ie, taking the motor as it is now, at 12 Nm, or 16Nm through the second gearing, would this be enough to lift the weight?
Sorry if this is hard to understand, or something that is normally very simple for you guys. (Automation and motors etc are not usually my kind of work).
Many thanks
Sirius.
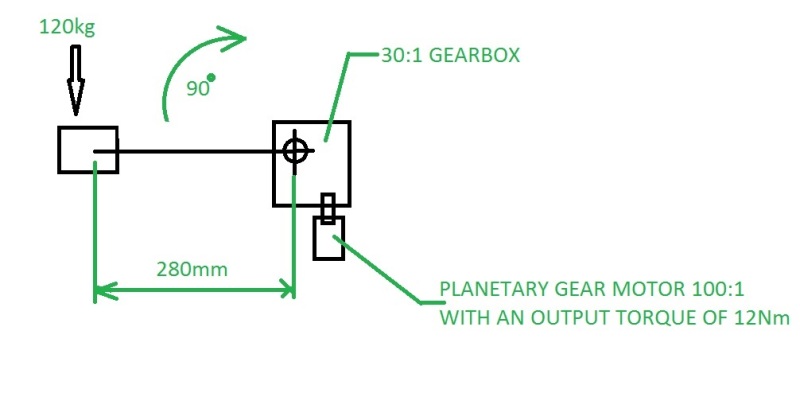