Alessandro Morelli
Mechanical
- Apr 27, 2022
- 4
Hi! My name is Aless, I am a Colombian Junior Mechatronic Engineer. I have a passion for CAD design and applied for my first job in the matter.
I got hired by a company, however, they want to test my design knowledge.
So I was given this problem of a staircase that the company produces by blocks of 6 stairs, the way they do bigger stairs is by connecting these 6 stair blocks in series by a joint in the middle using bolts (in the first image, the bolts are in the positions of the red lines drawn over the model, there are 8 of them holding the 3 pieces).
I was asked to design 4 possible variants of this joint in the 3D software, and point which bolts are under the biggest stress and give the stress numbers.
I have read the normativity, calculated dead stress and live stress on the staircase and have already calculated which distributed load the stairs should be able to withstand and under what safety factor.
Once I have the bolt forces calculated I know I will be able to calculate stress and design variants in no time, however, the knowledge of how to find the forces in the first place escapes my memory.
They are implying this is a very simple calculation that is done by an experienced engineer in under 2 hours by hand and they won't allow me to use the software's built-in finite element analysis tool
Perhaps I just don't know which equations should be used in the first place.
I have tried free force diagram by separating the distributed load into 2 punctual forces (Fko1 and Fko2) and calculating for the 3 parts but it gives me a system of 16 equations and 16 variables (forces in X and Y for 8 bolts), which I doubt can be done in so little time by hand and no matrix calculator.
I have also looked into Bolt Group Calculations using the elastic method, however, the books I found only go as deep as having only one set of fixed grouped bolts on one side.
I would be forever thankful if there is an experienced engineer in the matter that could simply tell me which equations might be of interest to me in this case.
Or even a book I could look into.
I already know how to use the 3D software for design and simulation, I think that once I understand this calculation I will be able to do a great job at the company, if I manage to keep it...
Thanks a lot for reading and for the invaluable help, and have a nice day!
I got hired by a company, however, they want to test my design knowledge.
So I was given this problem of a staircase that the company produces by blocks of 6 stairs, the way they do bigger stairs is by connecting these 6 stair blocks in series by a joint in the middle using bolts (in the first image, the bolts are in the positions of the red lines drawn over the model, there are 8 of them holding the 3 pieces).
I was asked to design 4 possible variants of this joint in the 3D software, and point which bolts are under the biggest stress and give the stress numbers.
I have read the normativity, calculated dead stress and live stress on the staircase and have already calculated which distributed load the stairs should be able to withstand and under what safety factor.
Once I have the bolt forces calculated I know I will be able to calculate stress and design variants in no time, however, the knowledge of how to find the forces in the first place escapes my memory.
They are implying this is a very simple calculation that is done by an experienced engineer in under 2 hours by hand and they won't allow me to use the software's built-in finite element analysis tool
Perhaps I just don't know which equations should be used in the first place.
I have tried free force diagram by separating the distributed load into 2 punctual forces (Fko1 and Fko2) and calculating for the 3 parts but it gives me a system of 16 equations and 16 variables (forces in X and Y for 8 bolts), which I doubt can be done in so little time by hand and no matrix calculator.
I have also looked into Bolt Group Calculations using the elastic method, however, the books I found only go as deep as having only one set of fixed grouped bolts on one side.
I would be forever thankful if there is an experienced engineer in the matter that could simply tell me which equations might be of interest to me in this case.
Or even a book I could look into.
I already know how to use the 3D software for design and simulation, I think that once I understand this calculation I will be able to do a great job at the company, if I manage to keep it...
Thanks a lot for reading and for the invaluable help, and have a nice day!
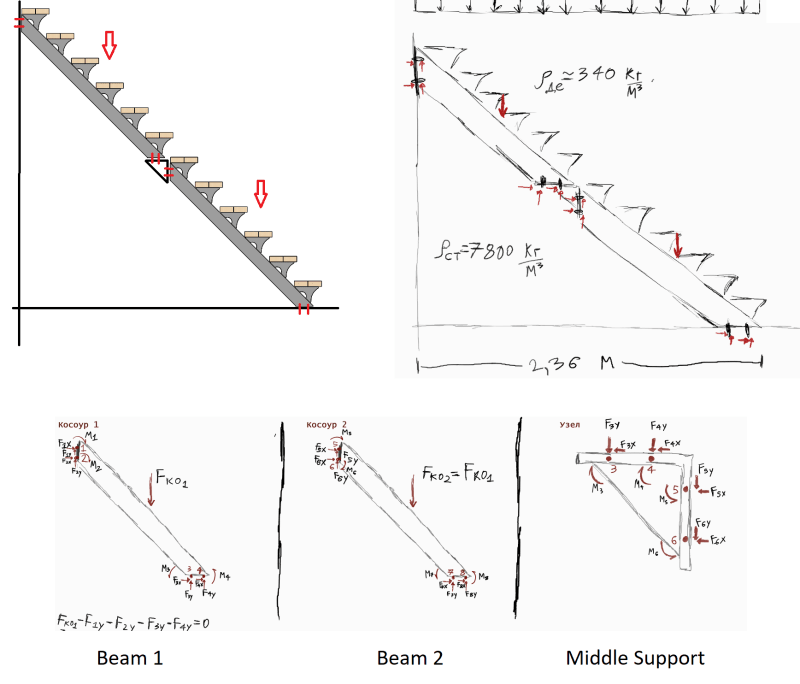