Hi all,
I am currently working on a lifting beam which has to be designed/analysed in accordance with BS13155:2020.
In the past, I have designed lifting beams which were based upon the clients own safety factor requirements and manuals, therefore BS13155 wasnt used as such.
The following is an extract from bs13155:2020 Annex A:
"A.1 Verification of mechanical strength by calculation
The mechanical strength shall be proven for the specific working load limit in accordance with
EN 13001-3-1.
The maximum permissible tilting angle specified for the attachment shall be taken into account in
calculations.
The design load used in calculations shall be derived using coefficients as given in 5.1.2 and 5.2 for both
yielded and elastic conditions.
The mechanical strength shall be calculated in accordance with EN 13001-1 and the limit design stress
shall be in accordance with:
— for the elastic condition, the allowable stress method;
— for the yielded condition, the limit state method."
§5.1.2 states that:
"5.1.2.1 Load lifting attachments designed for a maximum of 16 000 load cycles
— Elastic condition: the mechanical load bearing parts shall be designed to withstand a static load of
two times the load they are required to sustain under the intended operating conditions without
permanent deformation.
— Yielded condition: the mechanical load bearing parts shall be designed to withstand a static load of
three times the load they are required to sustain under the intended operating conditions without
releasing the load even if permanent deformation occurs.
The coefficients mentioned above cover the uncertainties of the value of the actual load and the impact
factor for hoisting a grounded load (dynamic effect) in general applications. The proof of fatigue strength
is not necessary, it is covered by the global safety of the proof of static strength."
As stated above, and referring to BS 13001-1, the limit state method for the yielded condition mentions dynamic factors, partial safety factors and risk coefficients to be applied to the applied loads.
So, based upon §5.1.2 (above), is BS13155 suggesting that these individual load factors/risk coefficients etc (from BS 13001-1) be replaced by a single load factor of 3 for the yielded condition? And the limit design stress (allowable stress) is material Ftu/1.10?
Regarding the allowable stress method for the elastic condition, where is the load factor of 2 (BS13155) applied? The admissible stress for this method equals the material Fty/(overall safety factor x risk coefficient).
I have attached snippets of the two stated methods.
Apologies if the answers are obvious but I want to make sure that I don't misinterpret the two methods and usage of load factors.
Thanks in advance
I am currently working on a lifting beam which has to be designed/analysed in accordance with BS13155:2020.
In the past, I have designed lifting beams which were based upon the clients own safety factor requirements and manuals, therefore BS13155 wasnt used as such.
The following is an extract from bs13155:2020 Annex A:
"A.1 Verification of mechanical strength by calculation
The mechanical strength shall be proven for the specific working load limit in accordance with
EN 13001-3-1.
The maximum permissible tilting angle specified for the attachment shall be taken into account in
calculations.
The design load used in calculations shall be derived using coefficients as given in 5.1.2 and 5.2 for both
yielded and elastic conditions.
The mechanical strength shall be calculated in accordance with EN 13001-1 and the limit design stress
shall be in accordance with:
— for the elastic condition, the allowable stress method;
— for the yielded condition, the limit state method."
§5.1.2 states that:
"5.1.2.1 Load lifting attachments designed for a maximum of 16 000 load cycles
— Elastic condition: the mechanical load bearing parts shall be designed to withstand a static load of
two times the load they are required to sustain under the intended operating conditions without
permanent deformation.
— Yielded condition: the mechanical load bearing parts shall be designed to withstand a static load of
three times the load they are required to sustain under the intended operating conditions without
releasing the load even if permanent deformation occurs.
The coefficients mentioned above cover the uncertainties of the value of the actual load and the impact
factor for hoisting a grounded load (dynamic effect) in general applications. The proof of fatigue strength
is not necessary, it is covered by the global safety of the proof of static strength."
As stated above, and referring to BS 13001-1, the limit state method for the yielded condition mentions dynamic factors, partial safety factors and risk coefficients to be applied to the applied loads.
So, based upon §5.1.2 (above), is BS13155 suggesting that these individual load factors/risk coefficients etc (from BS 13001-1) be replaced by a single load factor of 3 for the yielded condition? And the limit design stress (allowable stress) is material Ftu/1.10?
Regarding the allowable stress method for the elastic condition, where is the load factor of 2 (BS13155) applied? The admissible stress for this method equals the material Fty/(overall safety factor x risk coefficient).
I have attached snippets of the two stated methods.
Apologies if the answers are obvious but I want to make sure that I don't misinterpret the two methods and usage of load factors.
Thanks in advance
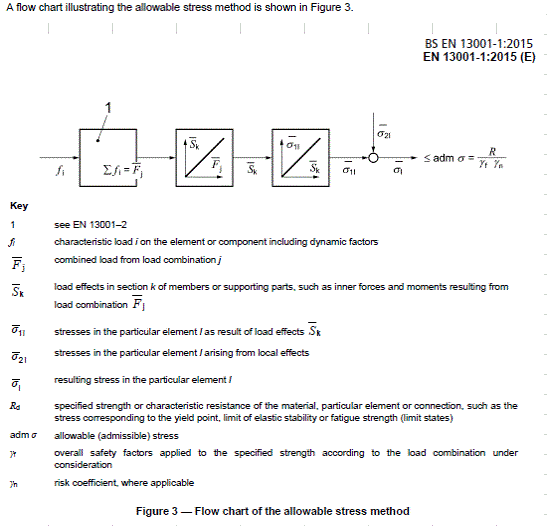
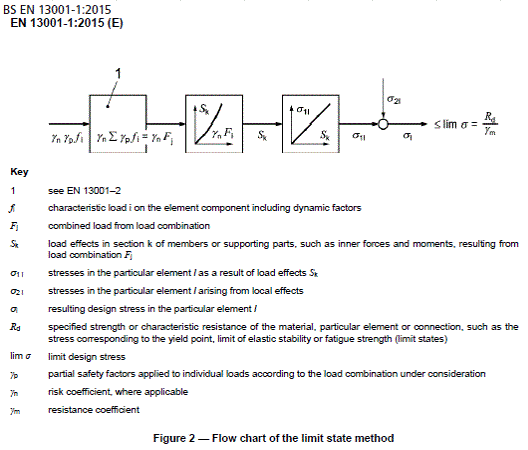