NickDePinhoPE
Mechanical
- Sep 27, 2024
- 2
Looking for some help on how to design the connections in this scenario. In this example shown I have an axial force of say 100lbs per each pipe. I need to design connections between my horizontal HSS and the building Ibeams.
How would I go about doing this? Typical I used unstiffened seated connections for deadweight loads. Any help or calculator I could use for this would be really helpful. I work with pipe supports I do not really need any information on connections that is beyond this scenario.
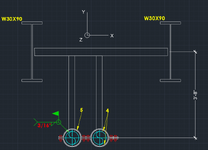
How would I go about doing this? Typical I used unstiffened seated connections for deadweight loads. Any help or calculator I could use for this would be really helpful. I work with pipe supports I do not really need any information on connections that is beyond this scenario.
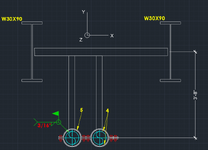