bottle77
Chemical
- Jul 29, 2019
- 21
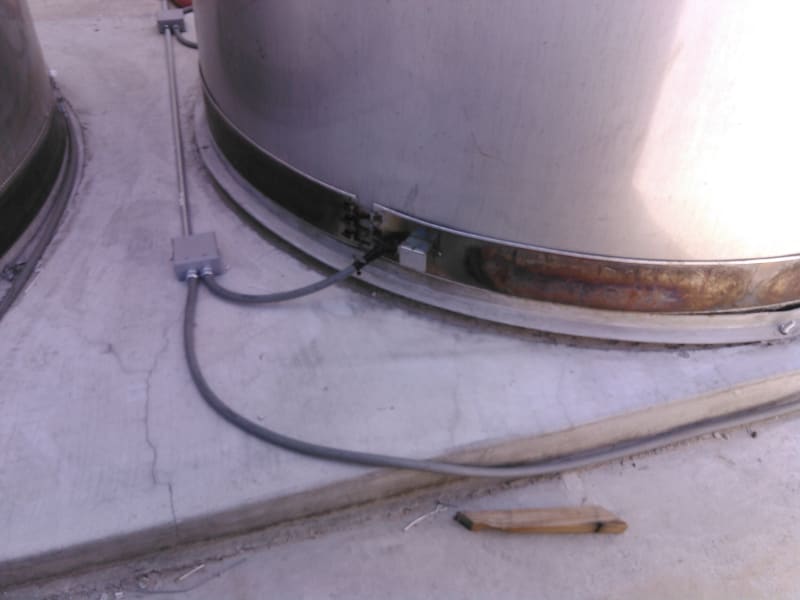
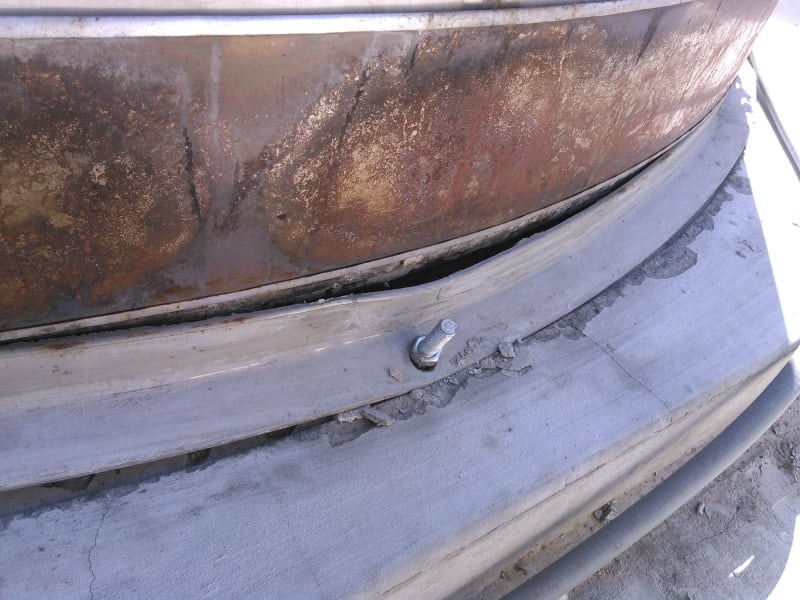
My company installed two 10,000 gal 304 SS tanks Just outside our plant back in
The tanks were installed about a foot apart on a level high strength concrete pad. 6 holes were drilled in the 2 inch angle iron flange around the tank bases and drilled down roughly 18" into the concrete. Then 24"x0.5" anchor bolts were epoxied into the holes and nuts were used to tighten the tank down to the concrete. After installation the tanks were equipped with band heaters at the bottom to help keep the material warm.
Last week the operators came in to find that the tank holding the 7.9 lb/gal liquid had snapped 3 of its bolts and bent a fourth considerably. Half of the base is sitting up 1.75". They emptied the 4,500 gallons of stored material out of it, and now we're trying to determine the cause of the failure, and how to remediate it. The other tank was just under half full at the time, probably also around 4,500gal.
Both tanks have vents to keep them at atmospheric pressure, so I don't think a pressure buildup could have caused this. The welds to the outer flange have been broken in a couple spots. The other tank doesn't really show any signs of stress, though there are some hairline cracks in the concrete around the flange. Could this be a failure from thermal expansion? The broken bolts appear to be sheared off. It was windy the evening it failed, but there was at least 35,000 Lbs of material sitting in the tank. I would think that would be enough to "hold it down" as it were. I would also think other parts of the tank would be damaged from wind before the base.
Any advice would be appreciated. Not sure where to start. If pictures of a different vantage point could help let me know. I am a recent grad with a ChemE degree. I don't know what analysis, if any, was done before they decided on how they wanted to install them outside of what was practical given space constraints. Tank schematic should be attached to the post