Hello everyone,
I need some help with a project I'm working on, the project is a remodeling of two condo units on top of each other in a 5-story condominium building, the client bought the unit on top of his old unit (2nd and 3rd floors) for the purpose of joining them vertically for a larger living area. The building was built in 2001, and there aren't any structural drawings available. the ground floor is an open parking garage concrete moment frame (flood zone), and the rest of the stories are CMU walls supported. the floors are made of 8" Hollow Core Slabs and 3.5" to 4" Field topping. Reinforcement of HCS is unknown, we tried investigating with a GPR, However, due to the topping thickness it's hard to tell how many strands or the size of the strands. the HCS are 8' in width.
We need to make an opening of approx. 5'x5' in the 3rd floor for the stair in the location shown in the picture, the dilemma is:
1. the building is 65' in width and there is no way to tell if it's one slab that spans the full width, two slabs or 4 slabs. (Assuming this will be needed for capacity verification).
2. with the reinforcement unknown, how would you go about verifying the HCS to support the spiral stair or the ability to make the opening.
My initial thought was to make a full width cut in one slab (8' x 5') next to a CMU wall and support the other end with a hanger to the adjacent slabs, but I'm not sure how I would go about verifying the capacity of the adjacent slabs to carry the slab I'm cutting without knowing the strand pattern, number, size and pretension stress. Also verifying the 2nd floor HCS can carry the spiral stairs main post / column.
the attached pictures show a plan view of the building with the approximate location of the stairs, a section view and the Hanger detail I mentioned.
Any ideas, suggestions or references would be greatly appreciated.
thank you!
MSc in Structural Engineering, PE
I need some help with a project I'm working on, the project is a remodeling of two condo units on top of each other in a 5-story condominium building, the client bought the unit on top of his old unit (2nd and 3rd floors) for the purpose of joining them vertically for a larger living area. The building was built in 2001, and there aren't any structural drawings available. the ground floor is an open parking garage concrete moment frame (flood zone), and the rest of the stories are CMU walls supported. the floors are made of 8" Hollow Core Slabs and 3.5" to 4" Field topping. Reinforcement of HCS is unknown, we tried investigating with a GPR, However, due to the topping thickness it's hard to tell how many strands or the size of the strands. the HCS are 8' in width.
We need to make an opening of approx. 5'x5' in the 3rd floor for the stair in the location shown in the picture, the dilemma is:
1. the building is 65' in width and there is no way to tell if it's one slab that spans the full width, two slabs or 4 slabs. (Assuming this will be needed for capacity verification).
2. with the reinforcement unknown, how would you go about verifying the HCS to support the spiral stair or the ability to make the opening.
My initial thought was to make a full width cut in one slab (8' x 5') next to a CMU wall and support the other end with a hanger to the adjacent slabs, but I'm not sure how I would go about verifying the capacity of the adjacent slabs to carry the slab I'm cutting without knowing the strand pattern, number, size and pretension stress. Also verifying the 2nd floor HCS can carry the spiral stairs main post / column.
the attached pictures show a plan view of the building with the approximate location of the stairs, a section view and the Hanger detail I mentioned.
Any ideas, suggestions or references would be greatly appreciated.
thank you!
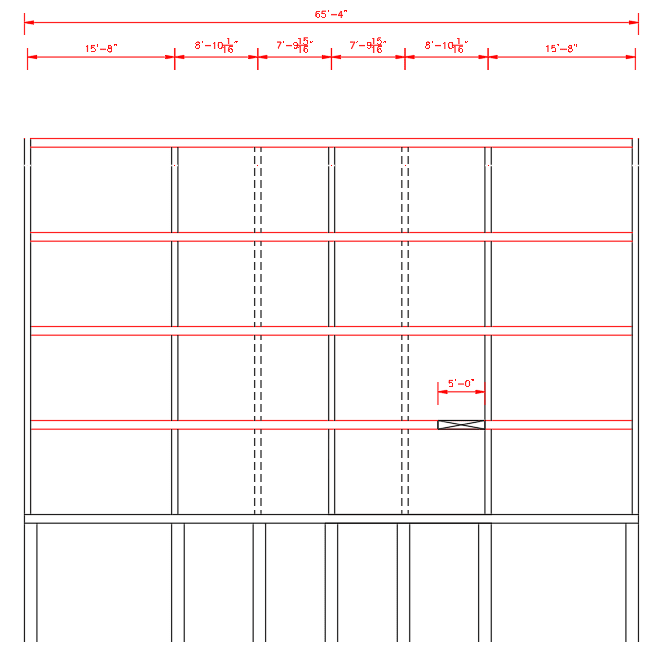
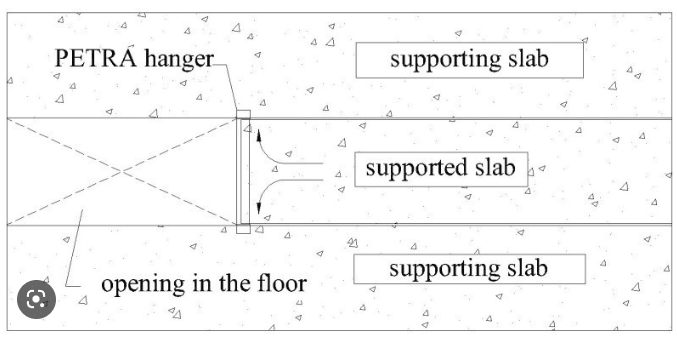
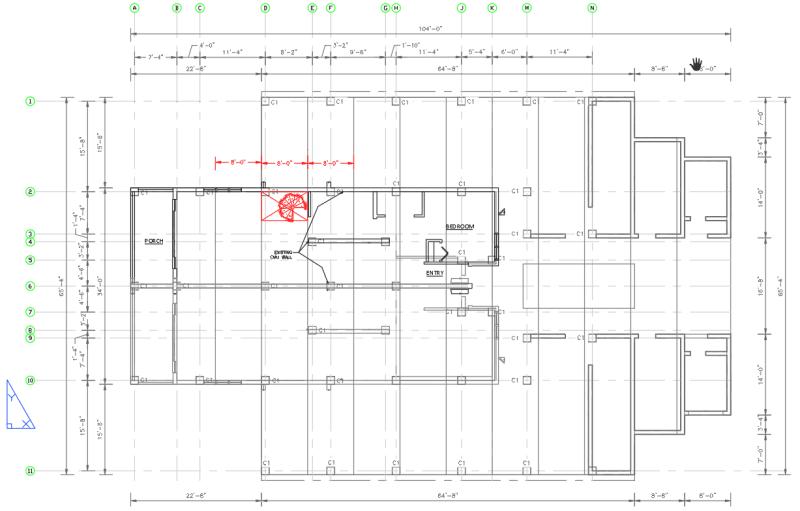
MSc in Structural Engineering, PE