UDDBOY
Petroleum
- Nov 27, 2017
- 8
How calculate corrosion allowance of HYDRAULIC TURBINE.
The information I have
1. Material is EN-JS1030 (QT400-15)Spheroidal graphite cast iron
2. Fluid is water (Chloride=220 ppm)
Thank You
The information I have
1. Material is EN-JS1030 (QT400-15)Spheroidal graphite cast iron
2. Fluid is water (Chloride=220 ppm)
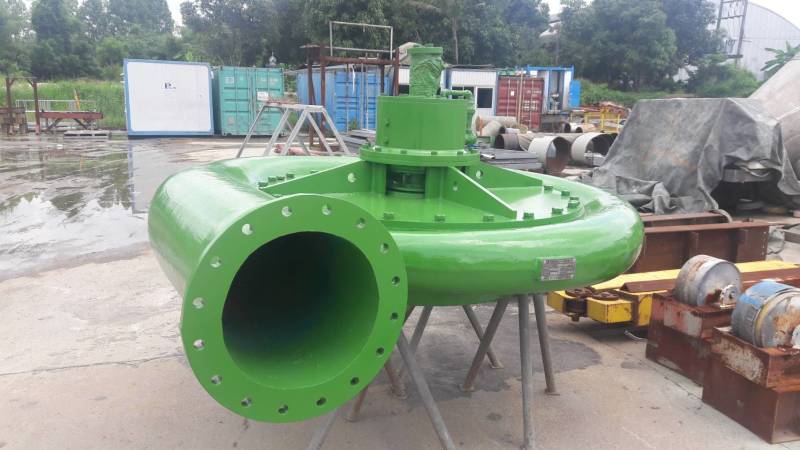
Thank You