Jay Prajapati
Mechanical
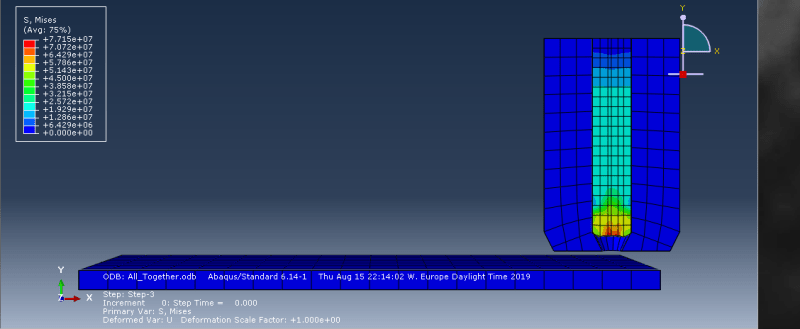
In my model I'm doing plastic extrusion simulation with motion of nozzle simultaneously. So material is flowing continuously and when material comes out of nozzle I want to add convection and conduction.
1)I want to do natural convection with melted material with the air. so how can I do interference melted semi solid part.
2) How to do conduction between glass plate and melted solid?
so how to manage interference of this to surfaces?