I am modeling a boxed item as shown in attached JPegs. I analyzed using shell elements and am getting high loads specifically at the T intersection shown. Item is bonded in place around all 4 faces so i put a fixed constraint at these locations. Is there a better way to analyze the problem, Maybe just do solid mesh and ensure at lease 3 elements at all thicknesses?
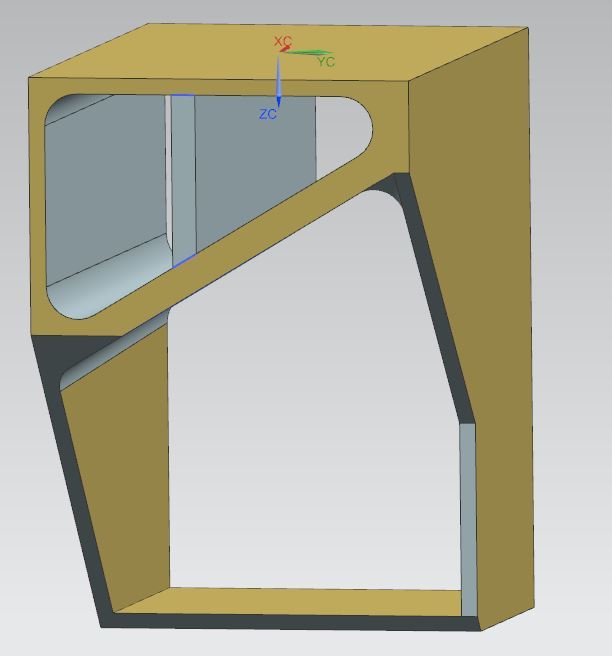
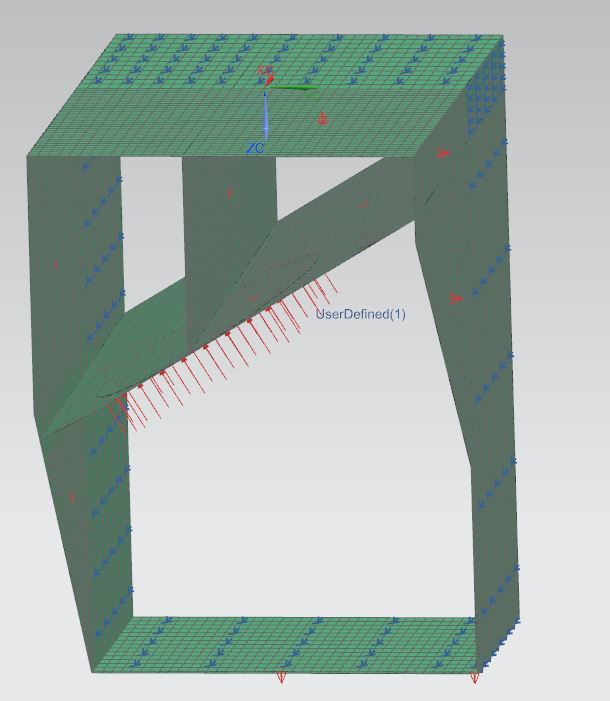
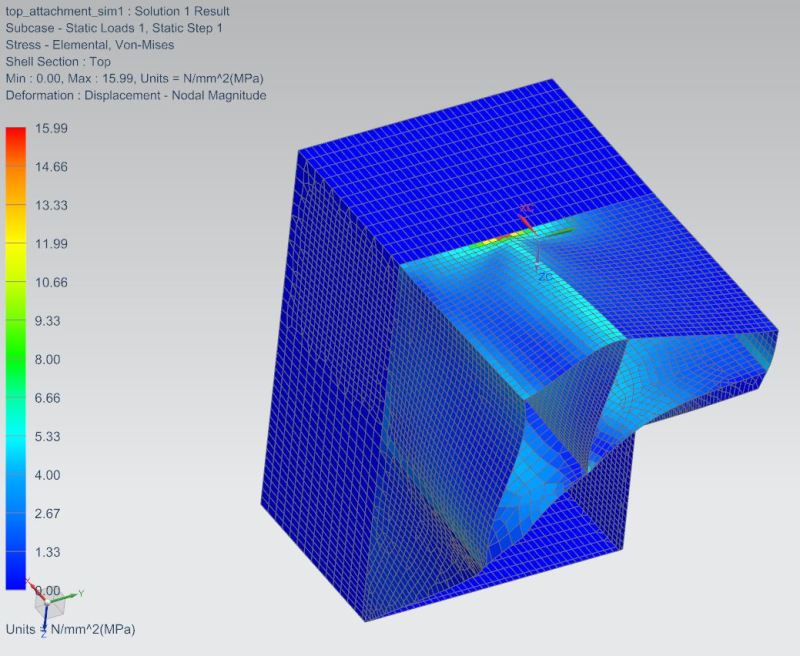