123nob
Geotechnical
- Dec 8, 2016
- 6
Hello;
I have as shown in the picture, a rope (in green), this rope is located between a support A and a support B. The Support A doesn't move and attached to the ground. The support B apply a force F1 against the rope, this force is made by a helical compression spring.
Because there is a friction between the rope and the two supports A and B, and because the spring push B toward A so we conclude that much the force F1 increase much it is harder to overcome the friction and move the rope.
The question is: How can I calculate the force F1 required to achieve a minimum overcome force T1 of 200 Newtons ? what I mean by this, is what characteristics the spring should have in order to generate a pushing force F1 that require at minimum 200 Newtons applied to the rope in order to move it ?
If the problem is difficult, may someone please give me a link to a similar problem to seek a solution.
Some data:
1. Coefficient of friction Rope/Support : u
2. Rope diameter : d
3. Weight of support B : Neglected
Thank You
I have as shown in the picture, a rope (in green), this rope is located between a support A and a support B. The Support A doesn't move and attached to the ground. The support B apply a force F1 against the rope, this force is made by a helical compression spring.
Because there is a friction between the rope and the two supports A and B, and because the spring push B toward A so we conclude that much the force F1 increase much it is harder to overcome the friction and move the rope.
The question is: How can I calculate the force F1 required to achieve a minimum overcome force T1 of 200 Newtons ? what I mean by this, is what characteristics the spring should have in order to generate a pushing force F1 that require at minimum 200 Newtons applied to the rope in order to move it ?
If the problem is difficult, may someone please give me a link to a similar problem to seek a solution.
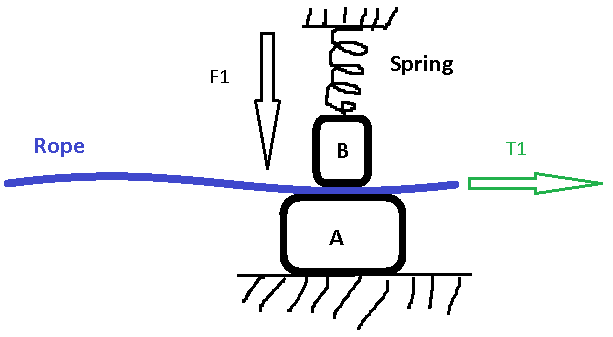
Some data:
1. Coefficient of friction Rope/Support : u
2. Rope diameter : d
3. Weight of support B : Neglected
Thank You