grahamrigs
Mechanical
So I'm designing a test rig in a hydraulic press. This is the general overview, the green is a section cut view.
The bottom plate is firmly attached to mounting holes on the press. The top plate will be pushed downwards by the press, compressing a not-necessarily flat object between it and the bottom plate. I need to ensure that the two plates remain as close as possible to parallel throughout the whole range of motion, which is maybe only an inch or two.
The only method to attach to the press' ram is a single 3/8" hole through the shaft. I've quickly modelled up the above image by assuming the top plate is attached to the ram with this bolt hole, but this isn't necessary if alignment is handled in another way (in fact, this may be preferred).
Just to kick off some ideas, here are small sketches of a linear guide system and a scissor system to ensure parallel.
Is there a simpler solution to this? The plates measure 24x24 inches (61x61 cm) and the press force will be up to 64 000 lbf (285 kN; equivalent of ~8 atmospheres of compaction pressure over the full area). These forces are within the capacity of the press, though barely.
Thanks for any help!
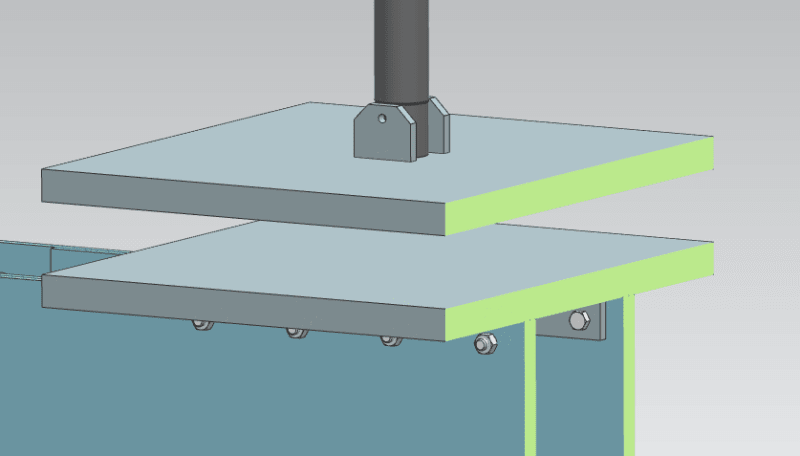
The bottom plate is firmly attached to mounting holes on the press. The top plate will be pushed downwards by the press, compressing a not-necessarily flat object between it and the bottom plate. I need to ensure that the two plates remain as close as possible to parallel throughout the whole range of motion, which is maybe only an inch or two.
The only method to attach to the press' ram is a single 3/8" hole through the shaft. I've quickly modelled up the above image by assuming the top plate is attached to the ram with this bolt hole, but this isn't necessary if alignment is handled in another way (in fact, this may be preferred).
Just to kick off some ideas, here are small sketches of a linear guide system and a scissor system to ensure parallel.
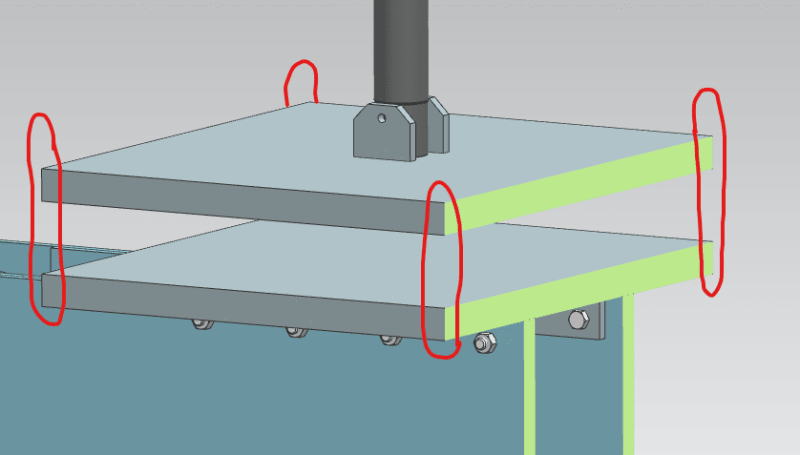
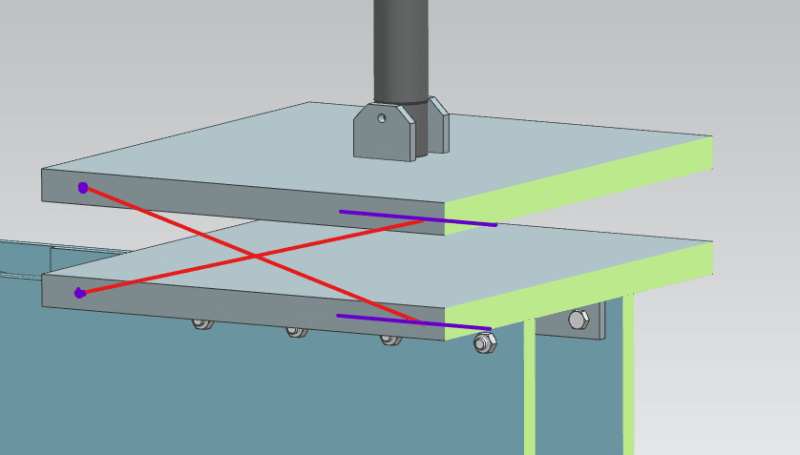
Is there a simpler solution to this? The plates measure 24x24 inches (61x61 cm) and the press force will be up to 64 000 lbf (285 kN; equivalent of ~8 atmospheres of compaction pressure over the full area). These forces are within the capacity of the press, though barely.
Thanks for any help!