YuJie_PV
Mechanical
- Jan 19, 2017
- 147
Hi, all experts,
i am dealing with a similar vessels like that in this post:
i dictate a simlilar design detail for the vessel under cyclic pressure on behalf of the owner.
and the manufacturer replied that it is unpractical for fabrication. the issues lie that, first, too much
buildup welding, second,the welding will definitely cause too much deformation of the bottom head.
if jtseng123 see the post, i'd like to know how did you accomplish your vessel finaly.
if anyone else who may experienced in the field, could you please shed some light on this issue?
Thanks so much.
i am dealing with a similar vessels like that in this post:
i dictate a simlilar design detail for the vessel under cyclic pressure on behalf of the owner.
and the manufacturer replied that it is unpractical for fabrication. the issues lie that, first, too much
buildup welding, second,the welding will definitely cause too much deformation of the bottom head.
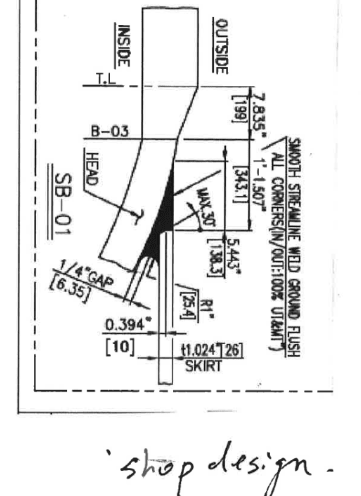
if jtseng123 see the post, i'd like to know how did you accomplish your vessel finaly.
if anyone else who may experienced in the field, could you please shed some light on this issue?
Thanks so much.