Hi ,someone please help me to get the capacity of a foot bracket
Objective : Find max capacity of the foot bracket(please refer the image for more details)
total bracket carrying load : 800N (80kg)
Softwares i use for FEA : Inventor & Solidworks
As i'm a designer , i'm not much involved in FEA before , please someone help me to find the capacity of this bracket
1. I don't know how to apply loads for this criteria and read the results of FEA like von mises stress contour plot and get the capacity, please explain me ?
2. I have attached the STEP files too
Kindly find the link to STEP file :
Objective : Find max capacity of the foot bracket(please refer the image for more details)
total bracket carrying load : 800N (80kg)
Softwares i use for FEA : Inventor & Solidworks
As i'm a designer , i'm not much involved in FEA before , please someone help me to find the capacity of this bracket
1. I don't know how to apply loads for this criteria and read the results of FEA like von mises stress contour plot and get the capacity, please explain me ?
2. I have attached the STEP files too
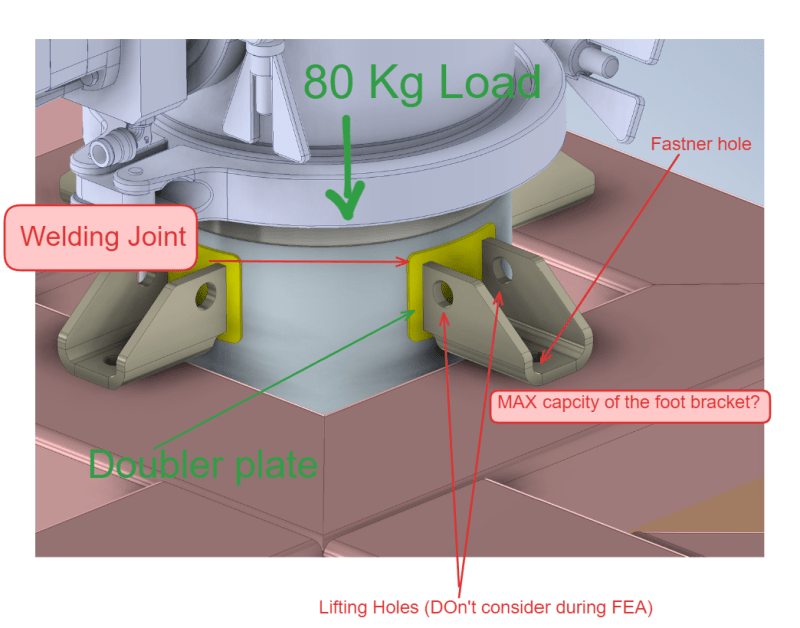
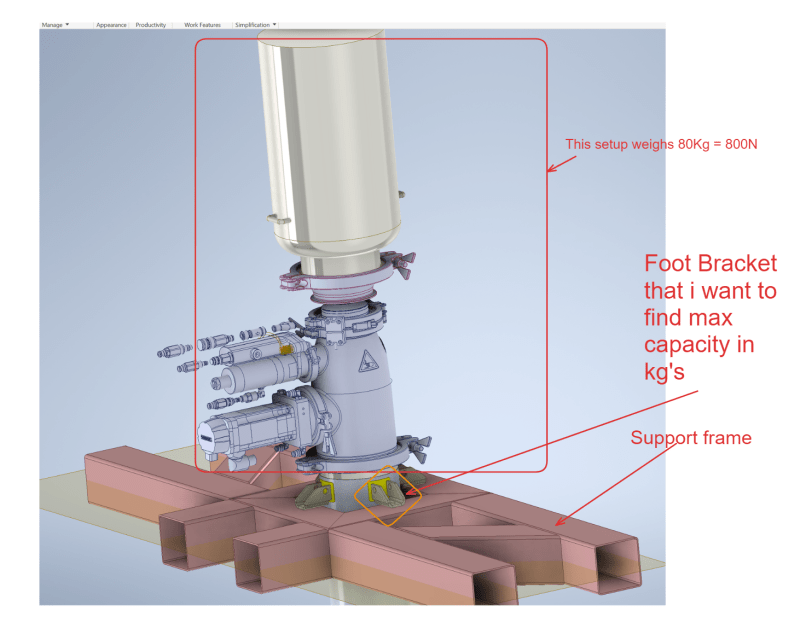
Kindly find the link to STEP file :