MatthewLynch
Mechanical
- May 27, 2024
- 10
Hi, I am trying to mesh some spot welds in NX on a beam that is made of a C section beam with a steel plate welded on the top and bottom. This is how I am meshing at the moment, I am meshing it all with CQUAD4 elements and they are 5mm in size (not inside the spot weld).
When I run the Element Quality check they all get a warning. But I can't find how to get NX to tell me what is causing the warning.
Is there a better aproach to meshing the spot weld? how can I know what causes the warning in the element quality to correct this?
Thank you
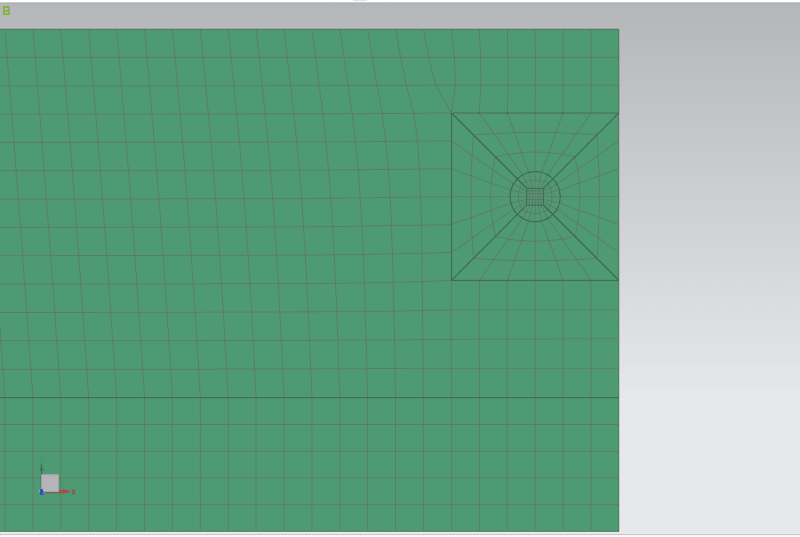
When I run the Element Quality check they all get a warning. But I can't find how to get NX to tell me what is causing the warning.
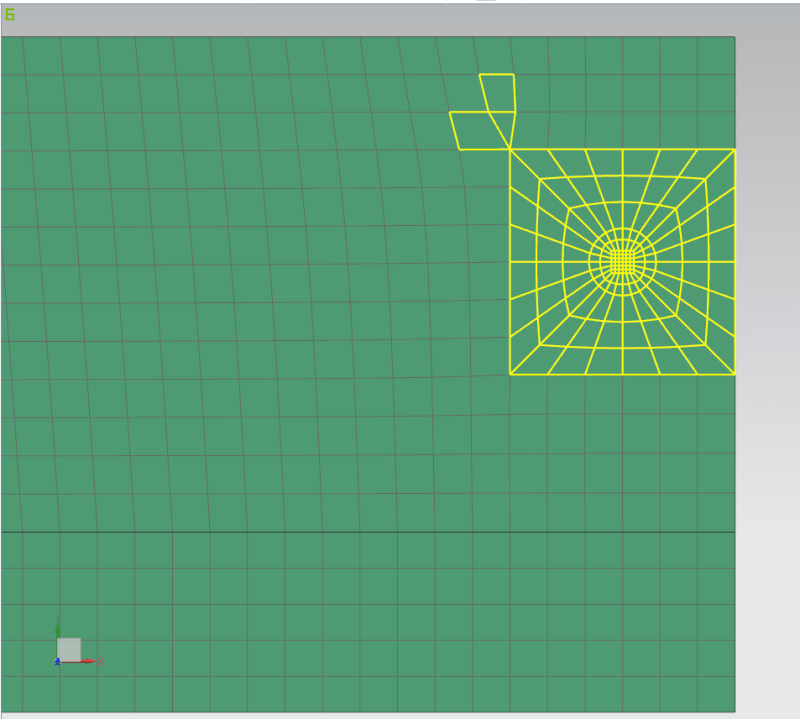
Is there a better aproach to meshing the spot weld? how can I know what causes the warning in the element quality to correct this?
Thank you