Good afternoon, I would like someone to help me with the following situation. I am modeling a piping system in CAESAR where the connections to the equipment are made with flexible hoses (a tight corrugated stainless steel tube with or without braided stainless steel mesh suitable for operating within a wide range of temperatures and pressures, capable of compensating for a variety of movements with excellent anti-corrosive properties. They are of annular type and manufactured according to ISO 10380 standard and their end fittings according to ISO 10806 standard).
What would be the best way to model this in CAESAR? Typically, where I work, they don't usually do it assuming that the flexible does not load the connection, so the model ends at the flexible connection flange instead of ending at the equipment connection. However, here is the detail of how I model that connection to be as realistic as possible. I was thinking of modeling it as an expansion joint and inputting the axial and transverse stiffness coefficients without adding the effective diameter, but the flexible supplier tells me they do not have the stiffness coefficients as they are very low and considered negligible, loading very little. What do you recommend I do?
"Attached are images of the flexible hoses. There are hoses for cryogenic service that are vacuum insulated, and others for gas, drains, and lubricating oil that are basically the same."
What would be the best way to model this in CAESAR? Typically, where I work, they don't usually do it assuming that the flexible does not load the connection, so the model ends at the flexible connection flange instead of ending at the equipment connection. However, here is the detail of how I model that connection to be as realistic as possible. I was thinking of modeling it as an expansion joint and inputting the axial and transverse stiffness coefficients without adding the effective diameter, but the flexible supplier tells me they do not have the stiffness coefficients as they are very low and considered negligible, loading very little. What do you recommend I do?
"Attached are images of the flexible hoses. There are hoses for cryogenic service that are vacuum insulated, and others for gas, drains, and lubricating oil that are basically the same."
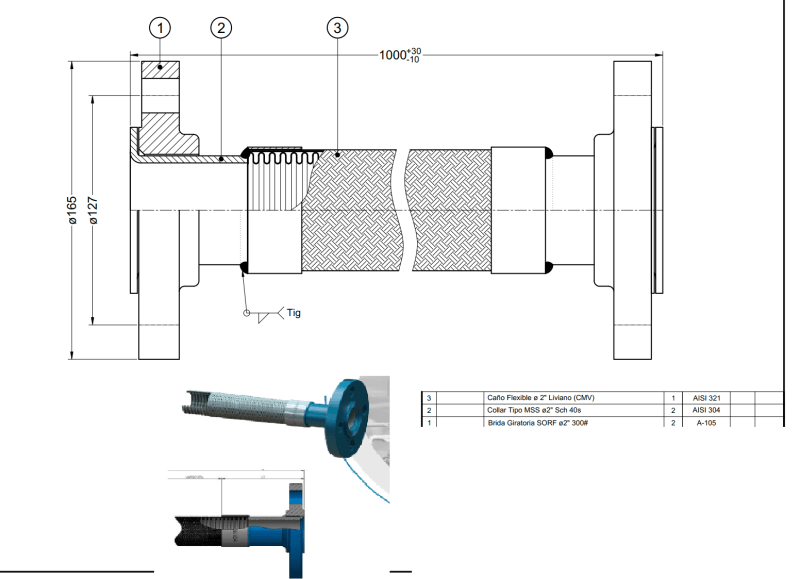
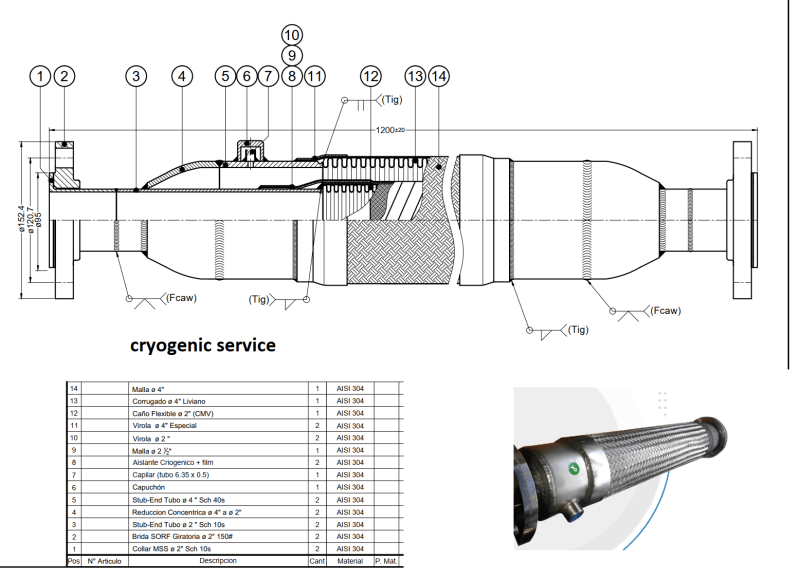