thelostelite
Mechanical
Hello,
I’m doing a project of something like the trunnion mechanism which is a motor that rotates another motor, which is perpendicular to the axis of rotation of the first motor…
I need some insight about how to do the hand calculations for it, eg; what type of stresses should I check for? And the deflection as well? I need these to verify whether my modeling approach is correct or not.
For the main axis, I put a torque load on the holes that supports the motor mount, then added a fixed geometry on the bearing side… is that correct?
This is a photo of the whole concept:
I divided the mechanism into two main parts, Main axis of rotation and the secondary axis of rotation:
Main Axis:
Secondary Axis:
I’m doing a project of something like the trunnion mechanism which is a motor that rotates another motor, which is perpendicular to the axis of rotation of the first motor…
I need some insight about how to do the hand calculations for it, eg; what type of stresses should I check for? And the deflection as well? I need these to verify whether my modeling approach is correct or not.
For the main axis, I put a torque load on the holes that supports the motor mount, then added a fixed geometry on the bearing side… is that correct?
This is a photo of the whole concept:
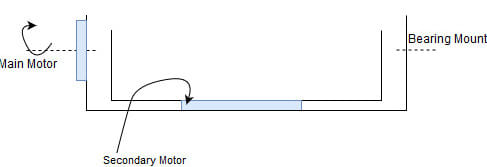
I divided the mechanism into two main parts, Main axis of rotation and the secondary axis of rotation:
Main Axis:
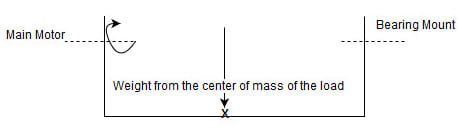
Secondary Axis:
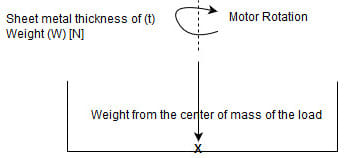