Imposter666
Mechanical
Hi,
Please see the attached image. We have this dust collector system that sucks metal dust from grinder(0.05mm-0.1mm)which gets mixed with water and gets kicked out from the bottom of the main vessel. When pump gets activated there is quite a turbulent flow inside the main vessel. On the side tube, we have 3 sensors for detecting high, low water levels and a float switch in the middle. These sensors don't last long in this hostile environment. I am thinking to put some sort of filter at Point A and Point B to prevent metal dust to pass to this side. However, it is important that water has free/uninterrupted movement with no lag here. Unfortunately the manufacturer doesn't have a countermeasure in place. Our application seems to be more "dirty" compared to what others use this system for. Is placing a filter at point A and B a good idea? If not, what can be done to prevent down time related to sensor malfunction? If filter idea is good, what type filter needs to be used here?
Thank you!
Please see the attached image. We have this dust collector system that sucks metal dust from grinder(0.05mm-0.1mm)which gets mixed with water and gets kicked out from the bottom of the main vessel. When pump gets activated there is quite a turbulent flow inside the main vessel. On the side tube, we have 3 sensors for detecting high, low water levels and a float switch in the middle. These sensors don't last long in this hostile environment. I am thinking to put some sort of filter at Point A and Point B to prevent metal dust to pass to this side. However, it is important that water has free/uninterrupted movement with no lag here. Unfortunately the manufacturer doesn't have a countermeasure in place. Our application seems to be more "dirty" compared to what others use this system for. Is placing a filter at point A and B a good idea? If not, what can be done to prevent down time related to sensor malfunction? If filter idea is good, what type filter needs to be used here?
Thank you!
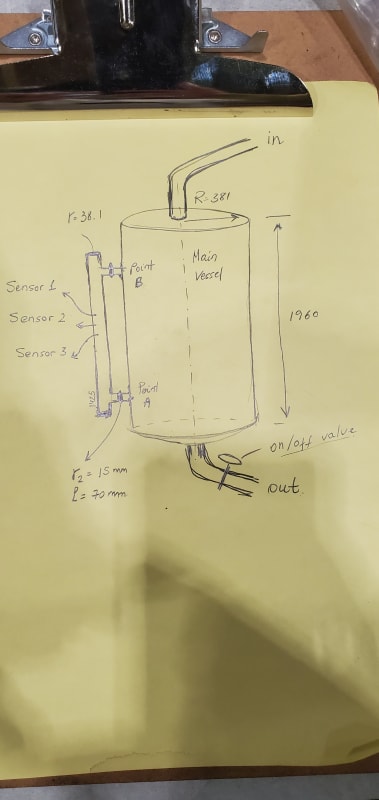