hi guys, I have a structural C channel rectangular base with 2 strips of angle iron going through the middle of the C channel base. Then I have a 1" square tubing that is placed on top of the Angle iron. I want to send this out to a machinist so I can get it built but not sure how to go about the Shop/machine drawings so they have the proper dimensions laid out.
Ill be sending my machinist the 3D cad model of the base and will start to work on the shop drawings for the base as well but I am getting different responses on how detailed I need to be with the shop drawings.
Here is an attached picture below of what the base looks like. How would you go about giving the proper dimensions for this when sending it to a machinist to build? All are standard metal parts.
Ill be sending my machinist the 3D cad model of the base and will start to work on the shop drawings for the base as well but I am getting different responses on how detailed I need to be with the shop drawings.
Here is an attached picture below of what the base looks like. How would you go about giving the proper dimensions for this when sending it to a machinist to build? All are standard metal parts.
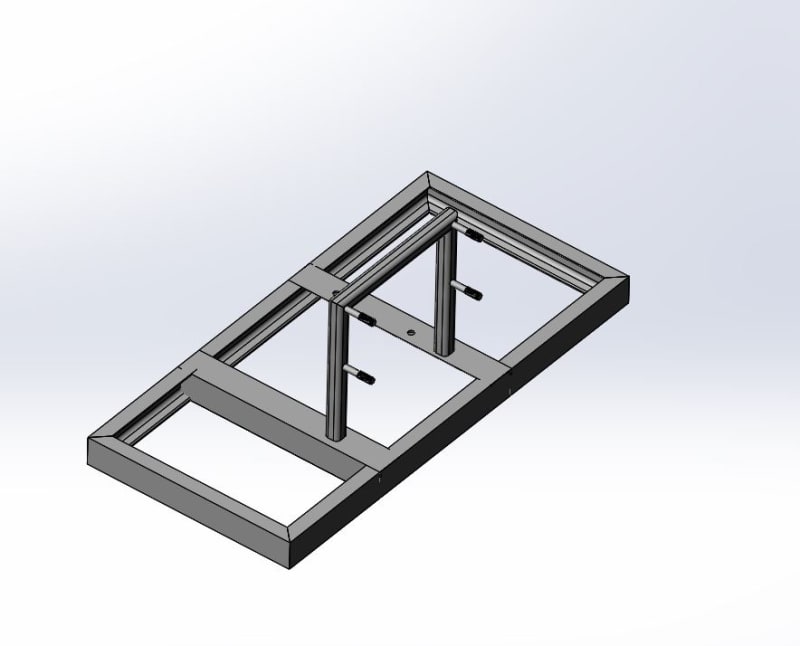