Hello
I am working with something that has me wondering how others would view this issue.
It concerns the glulam beam that you can see (simplified) in the figure bellow. It is a simply supported beam with an additional glulam "column" from 1 to 2. The blue lines are steel bars slightly prestressing the truss.
The load on the beam will result in tension in the steel and compression in the column. My impression from looking in different documents is that this structure is usually analyzed using beams or other line elements. But due to the circumstances I am using plate elements för the top beam. The figure is a simplification of reality but the top beam is 215 mm thick and 1.6 m high. What happens is that it buckles out of plane at location 2. And if I use non-linear analysis with initial imperfections I get a significant moment in the connection at 1. That of cource depends on the size of the imperfections.
My questioon is, how would you approach this structure? The reason I ask is because I can't see non-linear FEM-analysis as a typical design method. And I don't see how you can find this effect without it.
As always, ideas are appreciated.
Thomas
I am working with something that has me wondering how others would view this issue.
It concerns the glulam beam that you can see (simplified) in the figure bellow. It is a simply supported beam with an additional glulam "column" from 1 to 2. The blue lines are steel bars slightly prestressing the truss.
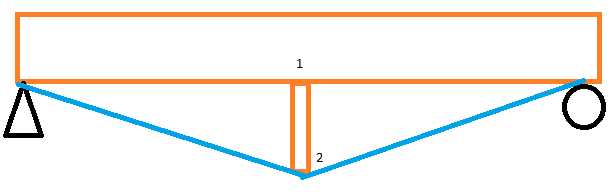
The load on the beam will result in tension in the steel and compression in the column. My impression from looking in different documents is that this structure is usually analyzed using beams or other line elements. But due to the circumstances I am using plate elements för the top beam. The figure is a simplification of reality but the top beam is 215 mm thick and 1.6 m high. What happens is that it buckles out of plane at location 2. And if I use non-linear analysis with initial imperfections I get a significant moment in the connection at 1. That of cource depends on the size of the imperfections.
My questioon is, how would you approach this structure? The reason I ask is because I can't see non-linear FEM-analysis as a typical design method. And I don't see how you can find this effect without it.
As always, ideas are appreciated.
Thomas