I've been looking at an issue here at my facility for the last 4 months or so. I'll start with some background, we have a GE LM6000 turbine with a EIT HRSG behind it. Back in June of this year, a loud intermittent banging was observed by one of our personnel. I began investigating that and found that cause after a bout 2 weeks (leak by on a blowdown line going to a flash tank would cause occasionally cause it under the right conditions). We resolved that issue; however, while I was investigating that issue, I found a much more frequent and severe water hammer happening every time we start the unit (we had 200+ starts in the last year).
When we startup, the feedwater line is pressurized against closed control valves (Class 5 or 6 shutoff). Exhaust gas begins to flow and heat the HRSG. During this time, the LP FW temp begins to drop (it typically loses about 120+ degrees). The temp probe is downstream of the closed LP FW control valve just before the water enters the drum. The water upstream of the control valve typically cools off while the unit is off, since the line comes from the economizer to the CV outside the unit, though it is insulated. To me, it seemed that leak by of the control was the most likely issue. We were introducing cold water from the line and flashing it across the CV. Additionally, the volume of water in the FW line that is external to the unit is ~50 gallons. I did some other testing where we pressurized the line and used the reading from the flow meter and it seemed to line up that once the cool water was evacuated from the line, the hammering stopped.
However, we did another test were we did not pressurize the FW line. We started the turbine and began heating the HRSG. During this test, the same temperature drop and water hammer were experienced. I have attached trends from both scenarios (top one is with pressurizing FW before firing the turbine) where you can see a slight increase in pressure in the FW, but nowhere near the normal operating pressure. I cannot figure out why this would occur. I have been in communication with the HRSG OEM and they do not seem to have any idea what may be causing it. I have sent them full data from all points on the HRSG and FW systems and they haven't come to any conclusions.
We also had the unit open for annual inspection last month and found the FW header inside the LP drum was completely loose from it's supports. I borescoped the pipe and didn't see anything that would concern me. We reattached the header to the supports and just started the unit last Friday with the same results as before (large drop at LP FW temp probe and water hammer). I also spoke with some of our senior maintenance people and they stated this has happened since the unit was new (about 7 years old), but it was never investigated. Since you can only hear it when you are halfway up the HRSG stair tower, nobody noticed or cared enough to look for a root cause.
I don't want to start throwing new components or doing mods to the unit unnecessarily. I still believe CV leak by is most likely cause. However, to confuse matters even more, we closed all the manual isolation valves at the CV station and pressurized the line. The same temperature drop downstream of the CV was observed, but no hammering occurred. I attached piping arrangement drawings from the economizer outlet to the LP drum inlet for review. All of that said, anyone have experience with anything like this?
When we startup, the feedwater line is pressurized against closed control valves (Class 5 or 6 shutoff). Exhaust gas begins to flow and heat the HRSG. During this time, the LP FW temp begins to drop (it typically loses about 120+ degrees). The temp probe is downstream of the closed LP FW control valve just before the water enters the drum. The water upstream of the control valve typically cools off while the unit is off, since the line comes from the economizer to the CV outside the unit, though it is insulated. To me, it seemed that leak by of the control was the most likely issue. We were introducing cold water from the line and flashing it across the CV. Additionally, the volume of water in the FW line that is external to the unit is ~50 gallons. I did some other testing where we pressurized the line and used the reading from the flow meter and it seemed to line up that once the cool water was evacuated from the line, the hammering stopped.
However, we did another test were we did not pressurize the FW line. We started the turbine and began heating the HRSG. During this test, the same temperature drop and water hammer were experienced. I have attached trends from both scenarios (top one is with pressurizing FW before firing the turbine) where you can see a slight increase in pressure in the FW, but nowhere near the normal operating pressure. I cannot figure out why this would occur. I have been in communication with the HRSG OEM and they do not seem to have any idea what may be causing it. I have sent them full data from all points on the HRSG and FW systems and they haven't come to any conclusions.
We also had the unit open for annual inspection last month and found the FW header inside the LP drum was completely loose from it's supports. I borescoped the pipe and didn't see anything that would concern me. We reattached the header to the supports and just started the unit last Friday with the same results as before (large drop at LP FW temp probe and water hammer). I also spoke with some of our senior maintenance people and they stated this has happened since the unit was new (about 7 years old), but it was never investigated. Since you can only hear it when you are halfway up the HRSG stair tower, nobody noticed or cared enough to look for a root cause.
I don't want to start throwing new components or doing mods to the unit unnecessarily. I still believe CV leak by is most likely cause. However, to confuse matters even more, we closed all the manual isolation valves at the CV station and pressurized the line. The same temperature drop downstream of the CV was observed, but no hammering occurred. I attached piping arrangement drawings from the economizer outlet to the LP drum inlet for review. All of that said, anyone have experience with anything like this?
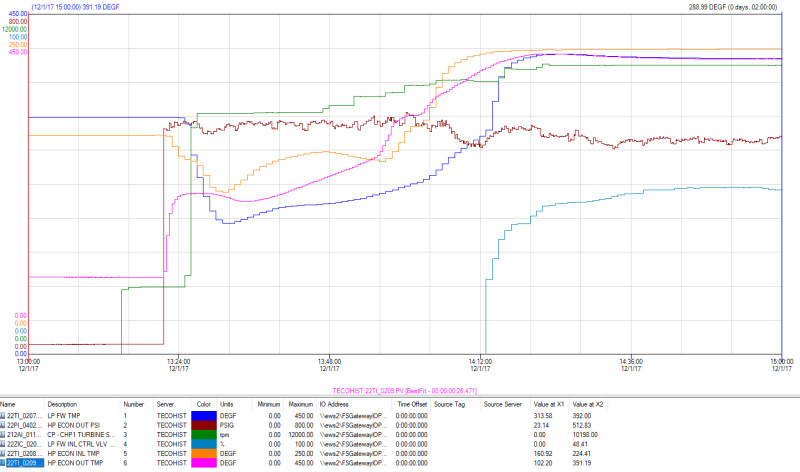
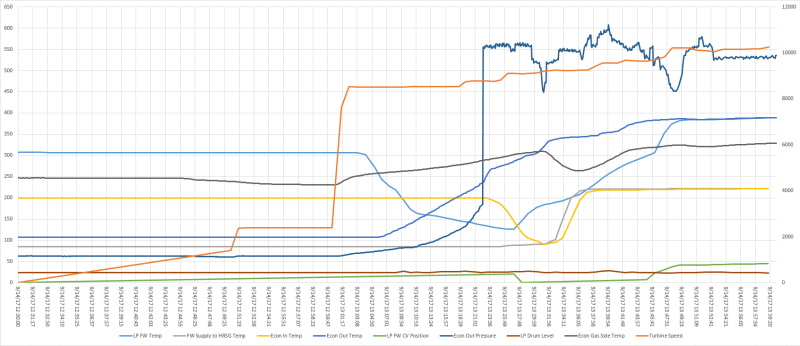