Guastavino
Structural
- Jan 29, 2014
- 381
Hi All,
KookK had a great thread last year about column dents, and I've run into a similar issue, but I'm thinking this one merits some repair. See below pics.
It's a 40' tall HSS10x10x3/16 in 50' square bays with a TPO roof, ie very light. The bottom 4' are what you see. Column appears plumb as I put a level on all sides.
Here are my repair thoughts, weld 3/4"x4" studs at 12" o/c on each side and encase it with concrete, either 2' diameter or 2'x2' square pier that has stirrups and vertical bars that are epoxy anchored into the "pier", ie concrete to fill slab cut out, below. My thoughts are that that will stabilize any buckling opportunity and transfer load as required.
Problem is, I don't feel like I can "design" check this. It's just judgement based that load can transfer to the studs around the bent areas and then back into the column at other studs and it will stabilize buckling etc.
What blinds spots do I have?
Thanks to all!
KookK had a great thread last year about column dents, and I've run into a similar issue, but I'm thinking this one merits some repair. See below pics.
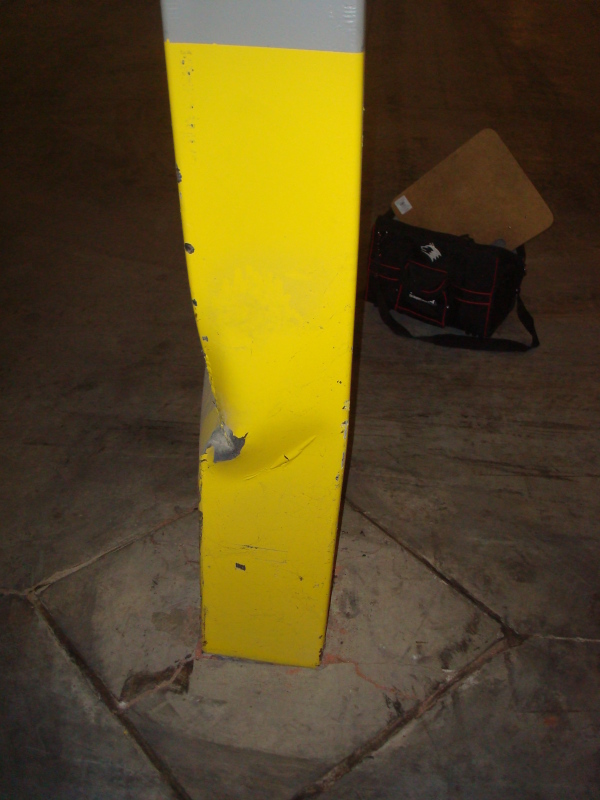
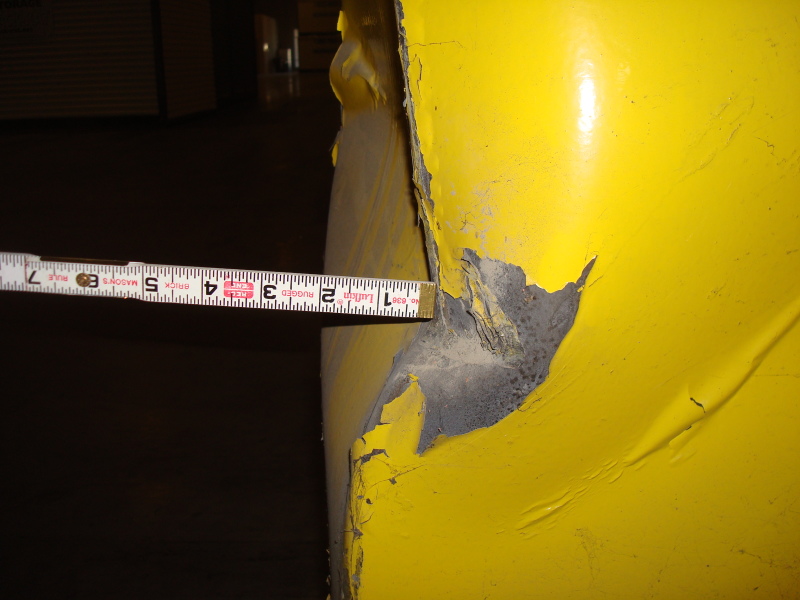

It's a 40' tall HSS10x10x3/16 in 50' square bays with a TPO roof, ie very light. The bottom 4' are what you see. Column appears plumb as I put a level on all sides.
Here are my repair thoughts, weld 3/4"x4" studs at 12" o/c on each side and encase it with concrete, either 2' diameter or 2'x2' square pier that has stirrups and vertical bars that are epoxy anchored into the "pier", ie concrete to fill slab cut out, below. My thoughts are that that will stabilize any buckling opportunity and transfer load as required.
Problem is, I don't feel like I can "design" check this. It's just judgement based that load can transfer to the studs around the bent areas and then back into the column at other studs and it will stabilize buckling etc.
What blinds spots do I have?
Thanks to all!