BEMPE16524
Mechanical
Dear All,
I have a confusion here. I have a working system like this,
Electrical motor:
RPM: 1500 @50Hz
Full load torque: 1651
Power: 250kW
Hyd pump:
Model: Eaton PVWS 360M (variable displacement)
flow: 360cc
Power consumption: 315kW @ 350Bar
Driving torque: 2005 @ 350Bar
above pump will drive a hydraulic motor below:
Hydraulic motor:
Model: Rextroth A6V (variable displacement)
displacement: 355cc
Max Torque: 1978 Nm
Max Speed: 2950RPM
So, our operating pressure is 220 Bar.
lpm @ 220 Bar of hydraulic pump = cc/rev x RPM / 1000 = 540lpm
@540lpm, the hydraulic motor will deliver 1344Nm and 2525RPM
When I calculate the hydraulic motor power base on this calculation they gave in their catalogue,
Power = 2 x 3.142 x T x RPM / 60,000 = 646HP = 482kW.
This Hydraulic motor is driving a submersible 3 stages water pump with following spec:
Head: 171m
speed: 2920 rpm
(see attachment for detail)
My question is, can that be possible? Hydraulic motor power is 482kW but the electrical motor is only 250kW? Sorry if I sound stupid, but that is a working system from a manufacturer which I can't trace them anymore. Or did I make false assumption some where?
TIA.
R.Efendy
I have a confusion here. I have a working system like this,
Electrical motor:
RPM: 1500 @50Hz
Full load torque: 1651
Power: 250kW
Hyd pump:
Model: Eaton PVWS 360M (variable displacement)
flow: 360cc
Power consumption: 315kW @ 350Bar
Driving torque: 2005 @ 350Bar
above pump will drive a hydraulic motor below:
Hydraulic motor:
Model: Rextroth A6V (variable displacement)
displacement: 355cc
Max Torque: 1978 Nm
Max Speed: 2950RPM
So, our operating pressure is 220 Bar.
lpm @ 220 Bar of hydraulic pump = cc/rev x RPM / 1000 = 540lpm
@540lpm, the hydraulic motor will deliver 1344Nm and 2525RPM
When I calculate the hydraulic motor power base on this calculation they gave in their catalogue,
Power = 2 x 3.142 x T x RPM / 60,000 = 646HP = 482kW.
This Hydraulic motor is driving a submersible 3 stages water pump with following spec:
Head: 171m
speed: 2920 rpm
(see attachment for detail)
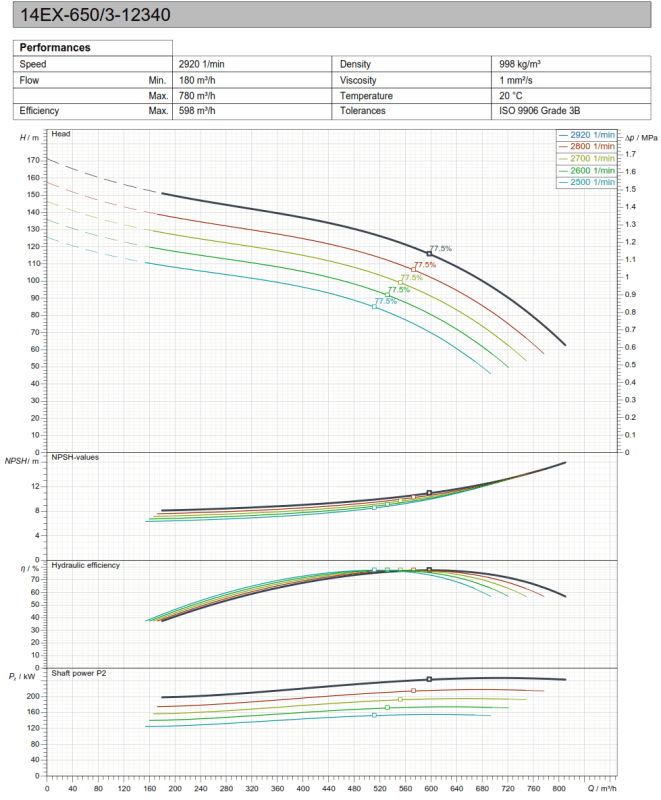
My question is, can that be possible? Hydraulic motor power is 482kW but the electrical motor is only 250kW? Sorry if I sound stupid, but that is a working system from a manufacturer which I can't trace them anymore. Or did I make false assumption some where?
TIA.
R.Efendy