Dear all,
Is it a bad thing to add a net to the hydraulic oil cooler fin side? The mesh can be pulled up for cleaning. The cooler is mounted on a crawler transporter to be used in sandy and muddy places (forest/plantation). The reason this decision was made because of wanting to clear off leaves and debris from the cooler fin.
A question was raised that it will make the cooling worse, and with operators not inspecting/cleaning this thing on a daily basis, it might just cook the hydraulic system.
What do you think?
Is it a bad thing to add a net to the hydraulic oil cooler fin side? The mesh can be pulled up for cleaning. The cooler is mounted on a crawler transporter to be used in sandy and muddy places (forest/plantation). The reason this decision was made because of wanting to clear off leaves and debris from the cooler fin.
A question was raised that it will make the cooling worse, and with operators not inspecting/cleaning this thing on a daily basis, it might just cook the hydraulic system.
What do you think?
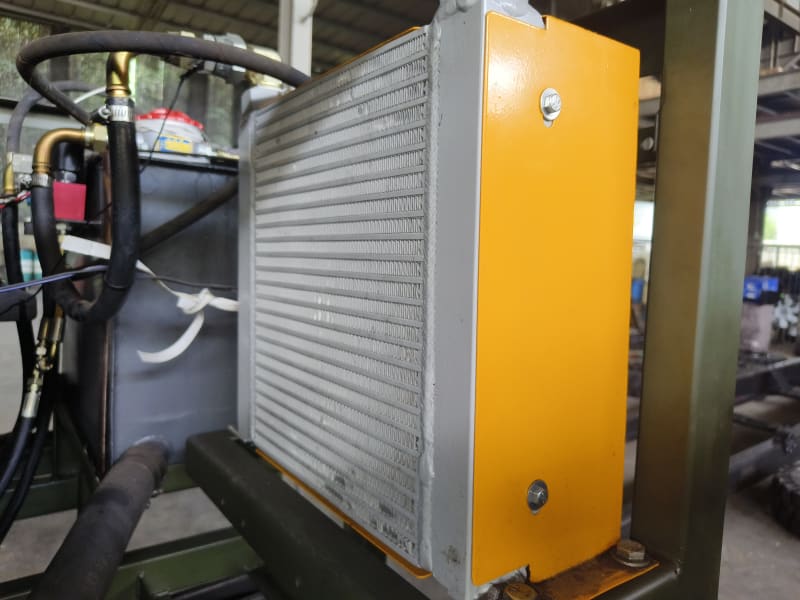
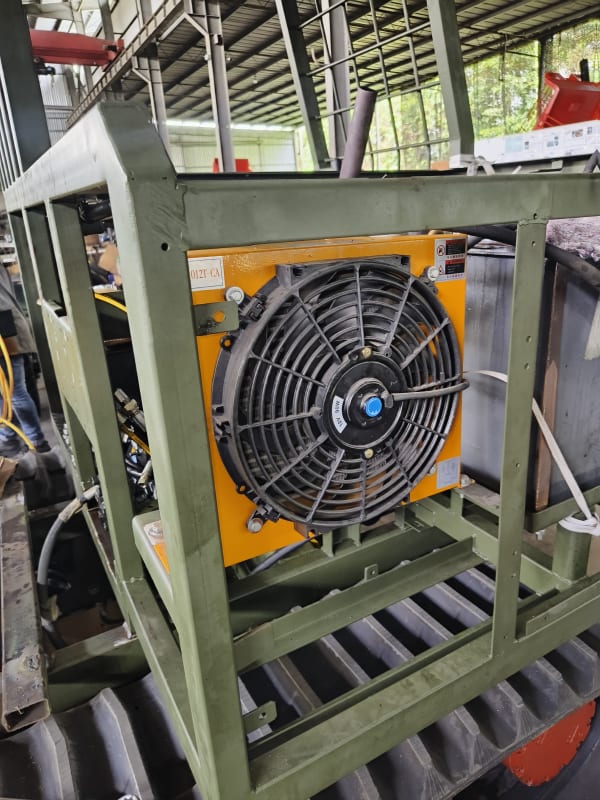
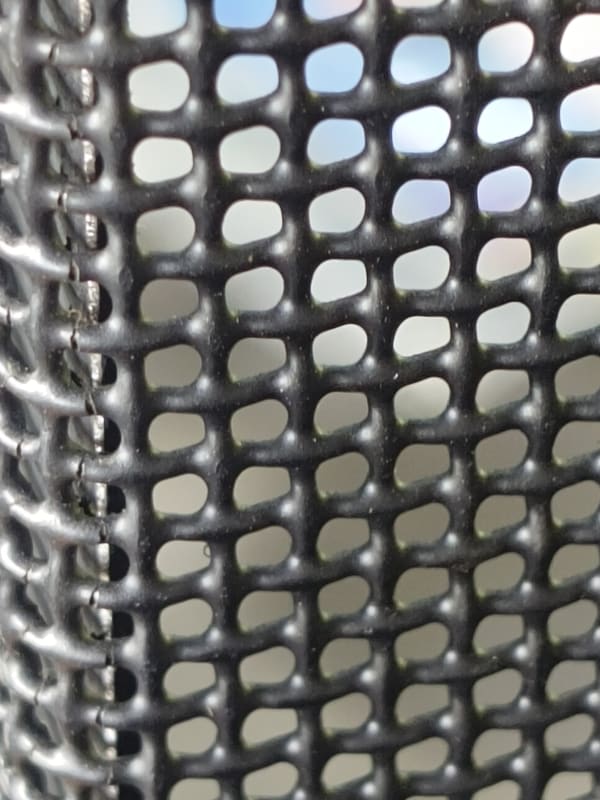
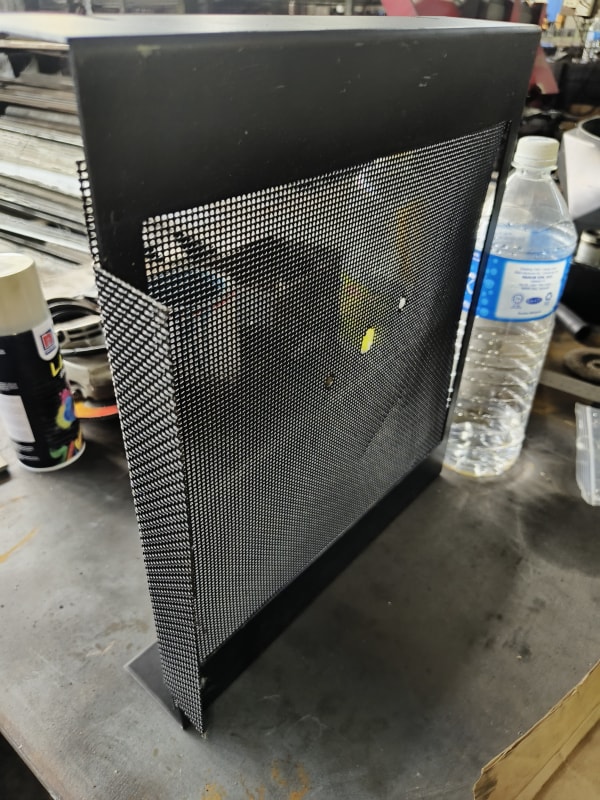
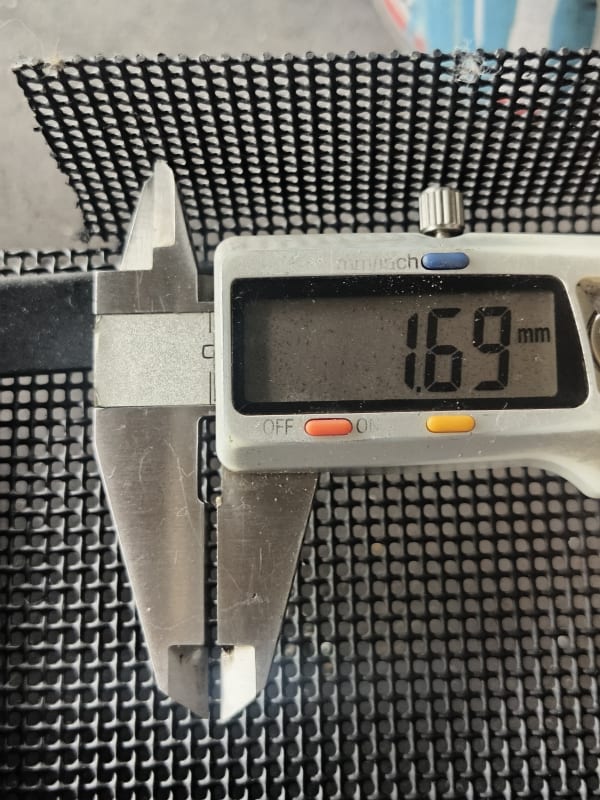
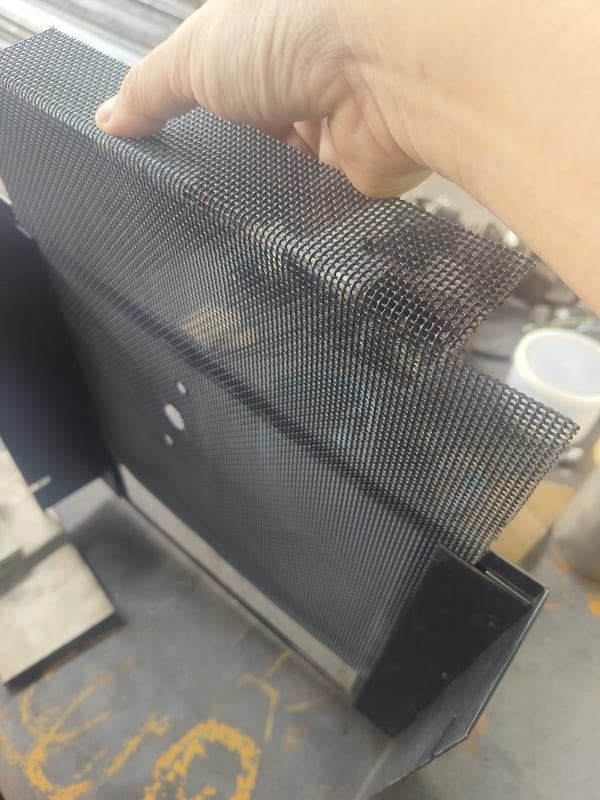