I came across a YouTube Video yesterday that has completely changed my thinking on hydrostatic testing vs. pneumatic testing. First, after a lot of digging, I found some of the details on the line:
[ul]
[li]ANSI 600 line[/li]
[li]Test was a fully degassed hydrostatic test (water for the test had been loaded 2 days before the test and allowed to degas)[/li]
[li]Tested to 130% of MAWP (1870 psig test pressure)[/li]
[li]All fittings and pipe were U.S. made[/li]
[li]All welds around the failure passed x-ray[/li]
[li]The line was owned by one of the largest pipeline companies in the U.S.[/li]
[li]The construction contractor had done hundreds of hydrostatic tests for that particular pipeline company and others[/li]
[li]The test was done following a procedure that had been reviewed both by the engineering contractor and the pipeline company[/li]
[/ul]
My eyeball is not well calibrated, but it looks like 30-inch pipe, but it might be smaller. I took a screen capture from the video to show the failure point
You can see from the picture that the failure started next to the weld, not in the weld.
I watched the video and asked myself "where did the energy come from to tear out a flap of steel and bend it up 90° against the curve of the pipe?" That was a huge force.
That is when I realized that the bulk modulus (i.e., the amount of pressure that would decrease the volume by 1%) of water is 319,000 psia, so to reach 1870 psig you would have to add 0.006% of the system volume. I looked at the enthalpy of the water at rest and the enthalpy of the water at test pressure and found a 5.3 BTU/lbm change. For a test that was more than a few joints long, W=m*ΔH+Δm*h turns out to be a really really big number. Archimedes Principle says that a force applied (or removed) from a closed volume will be transmitted everywhere within the closed volume, so this huge energy acts like a coiled spring that releases its entire energy at the failure point.
I've talked on this site many times about the errors in the NASA Glenn Research Methodology used by many to calculate the energy of a pneumatic test. Primarily my point has been that there is no way for distant mass to "know" about a failure and the mass that participates in a in a failure is limited to a few joints worth of gas.
The change in my position is that I've always been a bit defensive about the use of pneumatic tests, but I was wrong to be defensive. The energy available to strike nearby workers is far higher in a pipeline hydrostatic test than a pipeline pneumatic test. If we assume that the failure in the video was 5 miles of 30-inch pipe, then I calculate that the energy release in a pneumatic test would be 0.2% of the energy that could be released in a hydrostatic test. Yep, pneumatic tests are irresponsibly dangerous. NOT.
[bold]David Simpson, PE[/bold]
MuleShoe Engineering
In questions of science, the authority of a thousand is not worth the humble reasoning of a single individual. Galileo Galilei, Italian Physicist
[ul]
[li]ANSI 600 line[/li]
[li]Test was a fully degassed hydrostatic test (water for the test had been loaded 2 days before the test and allowed to degas)[/li]
[li]Tested to 130% of MAWP (1870 psig test pressure)[/li]
[li]All fittings and pipe were U.S. made[/li]
[li]All welds around the failure passed x-ray[/li]
[li]The line was owned by one of the largest pipeline companies in the U.S.[/li]
[li]The construction contractor had done hundreds of hydrostatic tests for that particular pipeline company and others[/li]
[li]The test was done following a procedure that had been reviewed both by the engineering contractor and the pipeline company[/li]
[/ul]
My eyeball is not well calibrated, but it looks like 30-inch pipe, but it might be smaller. I took a screen capture from the video to show the failure point
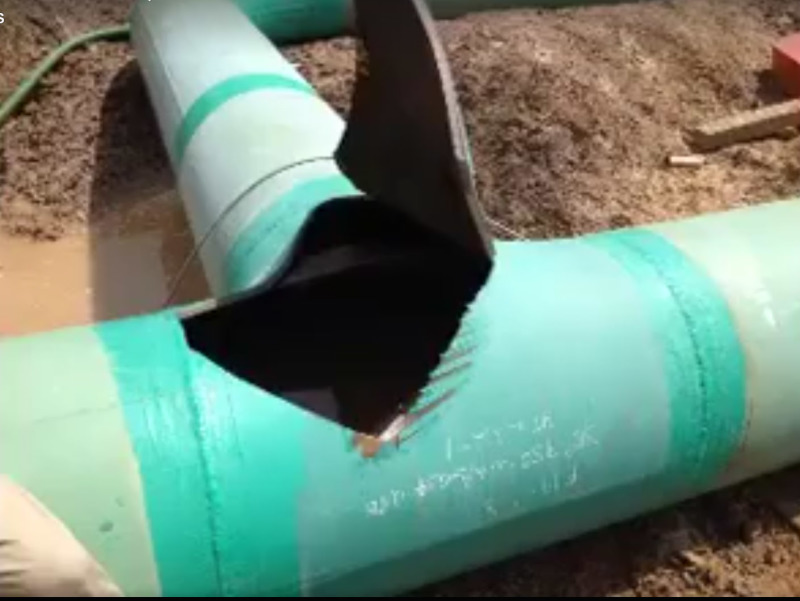
You can see from the picture that the failure started next to the weld, not in the weld.
I watched the video and asked myself "where did the energy come from to tear out a flap of steel and bend it up 90° against the curve of the pipe?" That was a huge force.
That is when I realized that the bulk modulus (i.e., the amount of pressure that would decrease the volume by 1%) of water is 319,000 psia, so to reach 1870 psig you would have to add 0.006% of the system volume. I looked at the enthalpy of the water at rest and the enthalpy of the water at test pressure and found a 5.3 BTU/lbm change. For a test that was more than a few joints long, W=m*ΔH+Δm*h turns out to be a really really big number. Archimedes Principle says that a force applied (or removed) from a closed volume will be transmitted everywhere within the closed volume, so this huge energy acts like a coiled spring that releases its entire energy at the failure point.
I've talked on this site many times about the errors in the NASA Glenn Research Methodology used by many to calculate the energy of a pneumatic test. Primarily my point has been that there is no way for distant mass to "know" about a failure and the mass that participates in a in a failure is limited to a few joints worth of gas.
The change in my position is that I've always been a bit defensive about the use of pneumatic tests, but I was wrong to be defensive. The energy available to strike nearby workers is far higher in a pipeline hydrostatic test than a pipeline pneumatic test. If we assume that the failure in the video was 5 miles of 30-inch pipe, then I calculate that the energy release in a pneumatic test would be 0.2% of the energy that could be released in a hydrostatic test. Yep, pneumatic tests are irresponsibly dangerous. NOT.
[bold]David Simpson, PE[/bold]
MuleShoe Engineering
In questions of science, the authority of a thousand is not worth the humble reasoning of a single individual. Galileo Galilei, Italian Physicist