Longfellowe
Electrical
I am working on a piece of vintage audio equipment from McIntosh that has damage to the chrome plated chassis from a leaking electrolytic capacitor.
The new capacitor will cover the damage cosmetically but I need to treat the chassis itself to prevent additional problems from rust and loss of more chrome going forward.
I’m good with the electronic part of this repair but my knowledge of metallurgy is abysmal. Any help and suggestions on a treatment/sealing regime would be greatly appreciated.
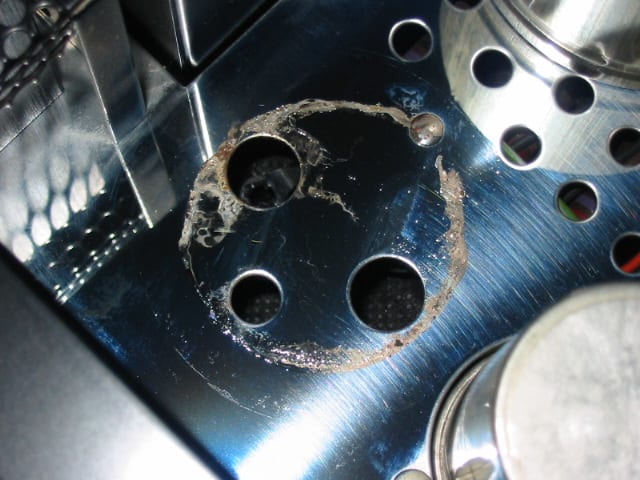
The new capacitor will cover the damage cosmetically but I need to treat the chassis itself to prevent additional problems from rust and loss of more chrome going forward.
I’m good with the electronic part of this repair but my knowledge of metallurgy is abysmal. Any help and suggestions on a treatment/sealing regime would be greatly appreciated.