Hi all, I wanna verify the model and therefore I checked whether the bending moment is same as theoretical value and found that there is huge difference.
SI unit defined: force=N, length=mm
Beam length:5000mm, flange width=100mm
Input load=200kN/m [I modeled as 19608N point load at each mesh node (100mm mesh, total 51 node)]
Bending moment should be SM2 and I understood SM2 is moment per unit width in Abaqus.
I tried to cut free body diaphragm near middle span(see below image)
The moment is 6.832e3.
The theoretical bending moment value should be 625kNm which is different from abaqus. But the theoretical reaction force is close to abaqus value.
I just wanna ask did I extract wrong moment or the model is wrong.
Thanks all
SI unit defined: force=N, length=mm
Beam length:5000mm, flange width=100mm
Input load=200kN/m [I modeled as 19608N point load at each mesh node (100mm mesh, total 51 node)]
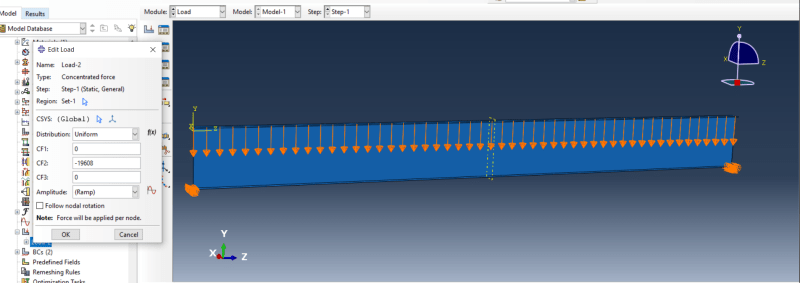
Bending moment should be SM2 and I understood SM2 is moment per unit width in Abaqus.
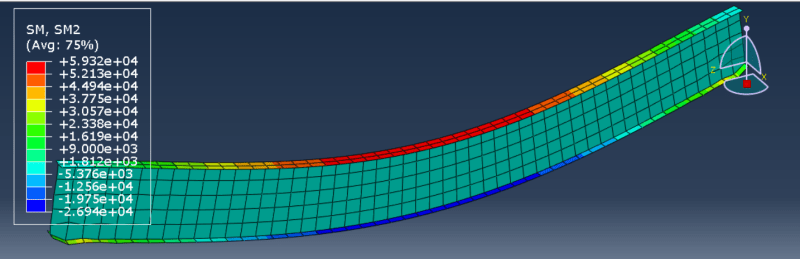
I tried to cut free body diaphragm near middle span(see below image)
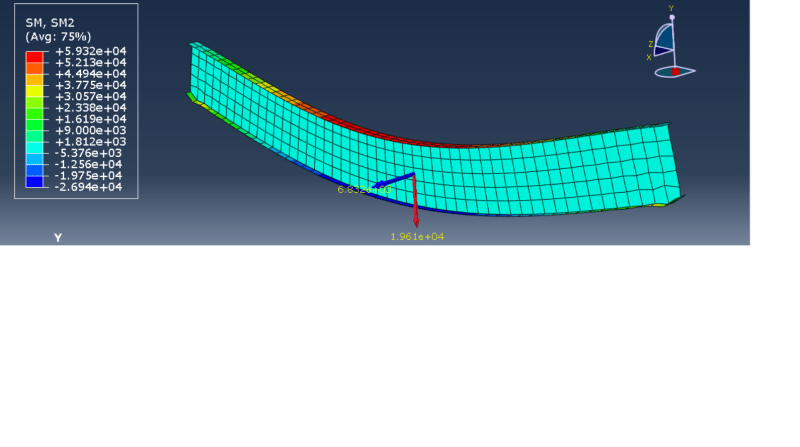
The moment is 6.832e3.
The theoretical bending moment value should be 625kNm which is different from abaqus. But the theoretical reaction force is close to abaqus value.
I just wanna ask did I extract wrong moment or the model is wrong.
Thanks all