Doodler3D
Mechanical
- Jan 20, 2020
- 188
Greetings Experts.
I am a new FEA engineer and have been tasked with a simple FEA analysis of a pressure containment vessel at 120 psi. The vessel has passed the EN 13445 standard but also needs ASME certification. My senior colleague has completed the ASME VIII Sec 1 calcs to approve the design. However, he's asked me to have a go at FEA and treat this task as if there was no ASME report to play with.
Material of Construction: SA240 ASME Stainless Steel 304L
Outlet flange thickness: 3/4"
Base thickness: 1"
Outlet duct plate thickness: 3/8"
Shell thickness: 1"
Rib thickness: 3/8"
Questions:
1. How should the flange be appropriately constrained?
2. Should I model welds?
3. Sub-modelling welds and ribs
4. Is pressure compensation important since I'm leaving the exit open? If not, do I need to cover it with a plate of relevant thickness?
Thank you.
I am a new FEA engineer and have been tasked with a simple FEA analysis of a pressure containment vessel at 120 psi. The vessel has passed the EN 13445 standard but also needs ASME certification. My senior colleague has completed the ASME VIII Sec 1 calcs to approve the design. However, he's asked me to have a go at FEA and treat this task as if there was no ASME report to play with.
Material of Construction: SA240 ASME Stainless Steel 304L
Outlet flange thickness: 3/4"
Base thickness: 1"
Outlet duct plate thickness: 3/8"
Shell thickness: 1"
Rib thickness: 3/8"
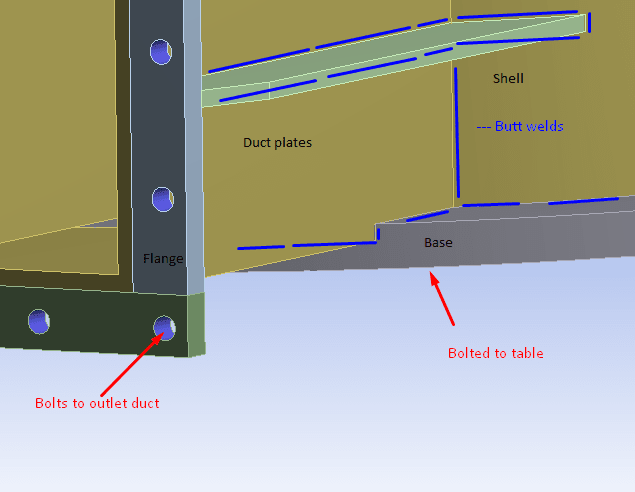
Questions:
1. How should the flange be appropriately constrained?
If I constrain the bolt holes or flange face, the stresses will increase. If the flange is left unconstrained, I may have unnecessary deflections.2. Should I model welds?
Since the welds are all butt welds, if I treat the structure as a bonded continuum, would that drastically increase stiffness. I've read that good butt welds and penetration welds have equivalent stiffness as the parent material, including the HAZ.3. Sub-modelling welds and ribs
How relevant it is to model welds on ribs as I expect stress concentrations to occur at the base of the ribs 4. Is pressure compensation important since I'm leaving the exit open? If not, do I need to cover it with a plate of relevant thickness?
Thank you.