Hello,
We recently designed some LDPE components that 1/4" NPT pipe threads. One component with internal threads and what component with external threads. We had molds made and received initial samples.
When tightening components together, the thread engagement feels sloppy. Before the components are fully tightened together, I can feel a small amount of play if I push/pull on the components. We compared this to existing off-the shelf products that use 1/4" NPT pipe threads, and this issue is not present in those. If we screw our male threads into the existing product female thread, and vice versa, the sloppiness improves, but the threads are still not mated as well as when using both existing products.
I am used to working with metal threads where we would check the threads with a plug gauge or ring gauge. Would this also be applicable when checking plastic threads? It seems that if the threads did not conform, the gauges would just deform them into complying, without me being able to validate the inspection.
I did examine the male threaded components with a microscope and overlayed the ideal thread profile in green. Our nozzle is top picture, existing off-the shelf nozzle is bottom picture.
As you can see, the crests and roots of our threads do not conform to the standard and I need to figure out why. Is this a machining issue in the mold, an issue with the injection process, or both? How should I go about correcting this issue with the mold maker, and what is the best method to inspect these threads upon arrival, other than the microscope?
I appreciate any help on this matter.
We recently designed some LDPE components that 1/4" NPT pipe threads. One component with internal threads and what component with external threads. We had molds made and received initial samples.
When tightening components together, the thread engagement feels sloppy. Before the components are fully tightened together, I can feel a small amount of play if I push/pull on the components. We compared this to existing off-the shelf products that use 1/4" NPT pipe threads, and this issue is not present in those. If we screw our male threads into the existing product female thread, and vice versa, the sloppiness improves, but the threads are still not mated as well as when using both existing products.
I am used to working with metal threads where we would check the threads with a plug gauge or ring gauge. Would this also be applicable when checking plastic threads? It seems that if the threads did not conform, the gauges would just deform them into complying, without me being able to validate the inspection.
I did examine the male threaded components with a microscope and overlayed the ideal thread profile in green. Our nozzle is top picture, existing off-the shelf nozzle is bottom picture.

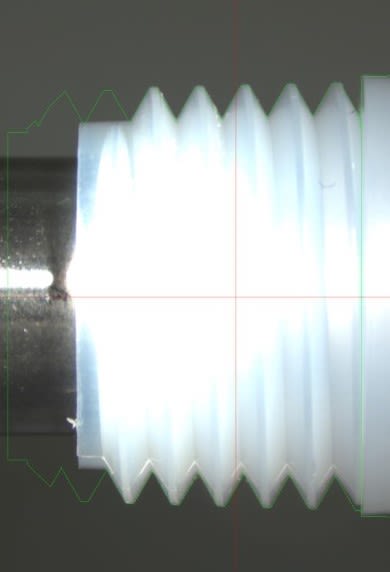
As you can see, the crests and roots of our threads do not conform to the standard and I need to figure out why. Is this a machining issue in the mold, an issue with the injection process, or both? How should I go about correcting this issue with the mold maker, and what is the best method to inspect these threads upon arrival, other than the microscope?
I appreciate any help on this matter.