-
1
- #1
Hello,
A colleague told me about a problem they had and how they decided to solve it, and I would like to find out what you think about it.
His crew designed a chamber (see a simplified picture below) that is expected to be flown and subjected to varied loads and vibration.
After getting all the parts and starting assembling they found out that the Safety Of Factor for side slippage (relative movement in x and/or z directions between both clamped parts of the chamber) is very small and marginal.
Since adding bolts (for increasing clamping force) was problematic, they decided they are going to increase the coefficient of friction between both clamped parts. They decided (without any experiment)to grit blast the mating surfaces like presented in the picture below.
I have several problems with their decision:
1. they damage the Hard Anodize surface treatment that should protect from corrosion, and abrasive grit blast would expose the aluminum.
2. they didn't really explored how much the coefficient of friction is increased and if it's worth it.
3. maybe there are more elegant solutions? maybe there is a specific surface treatment or coating that on one hand might increase the friction coefficient and on the other hand protect the metal from corrosion?
what is your opinion?
thanks!
A colleague told me about a problem they had and how they decided to solve it, and I would like to find out what you think about it.
His crew designed a chamber (see a simplified picture below) that is expected to be flown and subjected to varied loads and vibration.
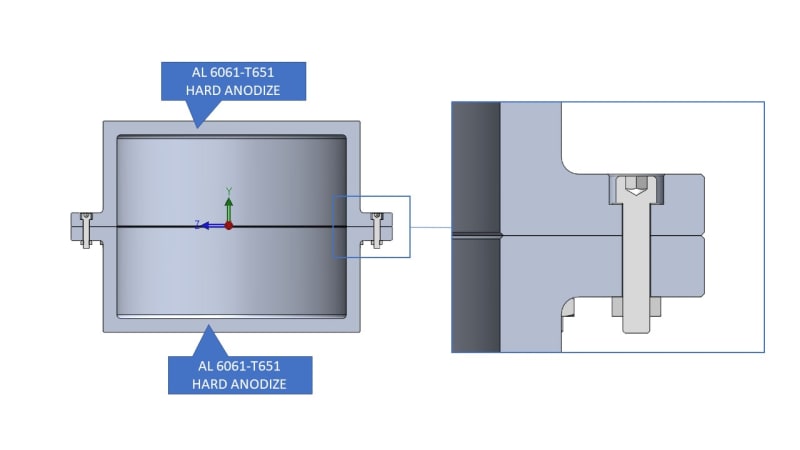
After getting all the parts and starting assembling they found out that the Safety Of Factor for side slippage (relative movement in x and/or z directions between both clamped parts of the chamber) is very small and marginal.
Since adding bolts (for increasing clamping force) was problematic, they decided they are going to increase the coefficient of friction between both clamped parts. They decided (without any experiment)to grit blast the mating surfaces like presented in the picture below.
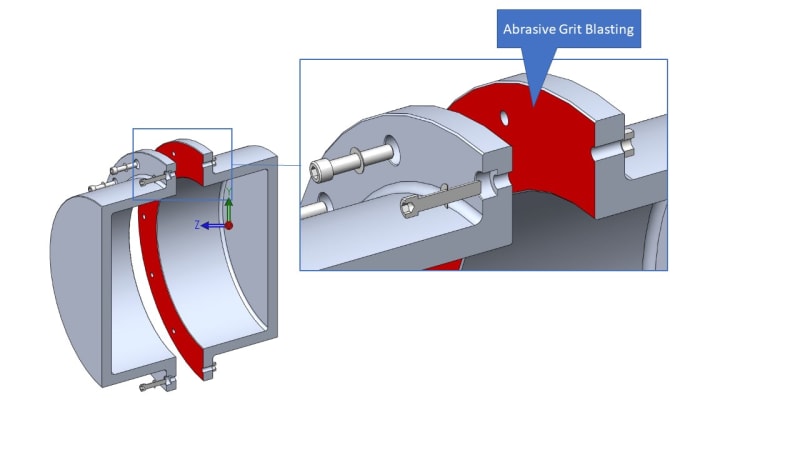
I have several problems with their decision:
1. they damage the Hard Anodize surface treatment that should protect from corrosion, and abrasive grit blast would expose the aluminum.
2. they didn't really explored how much the coefficient of friction is increased and if it's worth it.
3. maybe there are more elegant solutions? maybe there is a specific surface treatment or coating that on one hand might increase the friction coefficient and on the other hand protect the metal from corrosion?
what is your opinion?
thanks!