HDStructural
Structural
- Apr 24, 2024
- 118
Hello all,
I have an existing girder that is getting an increased load. After analyzing the existing shear connection, I have found it to be 60k short (about 13% too low). I am wondering if there are any implications to adding another shear tab or double angle connection below the existing connection to take the additional 60k.
My gut is that adding another 3 rows of long slotted horizontal bolts in a double angle connection would work well. I think that rotation compatibility would still be okay since we are not engaging the flanges of the girder and there would be long slotted horizontal holes in the angles.
What are your thoughts?
I have an existing girder that is getting an increased load. After analyzing the existing shear connection, I have found it to be 60k short (about 13% too low). I am wondering if there are any implications to adding another shear tab or double angle connection below the existing connection to take the additional 60k.
My gut is that adding another 3 rows of long slotted horizontal bolts in a double angle connection would work well. I think that rotation compatibility would still be okay since we are not engaging the flanges of the girder and there would be long slotted horizontal holes in the angles.
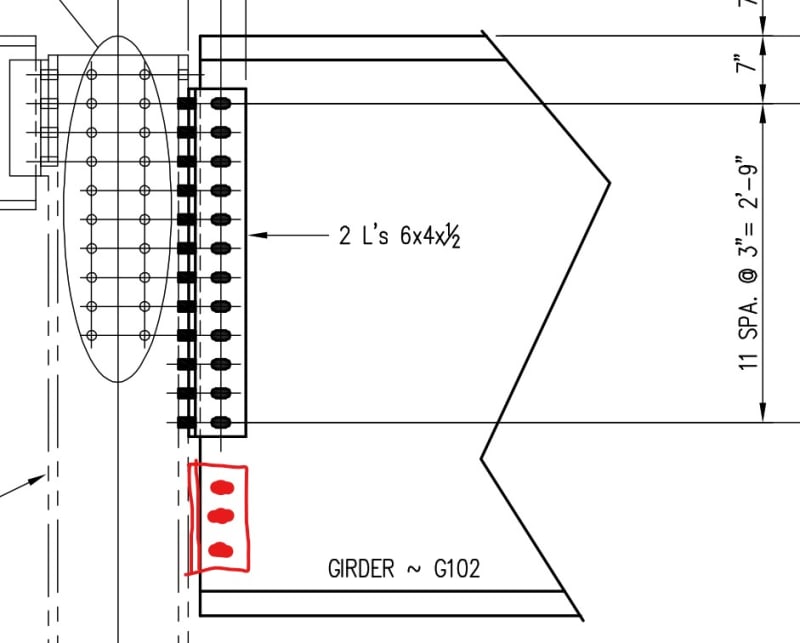
What are your thoughts?