Recently, we had to analyze a Tension T-Fitting for a client and we were getting negative margins at DLL. The client suggested that we could use plastic bending allowable instead of Fty and show it good. We performed the calc and it got me thinking.
How would be the behavior of a fitting/structure which has undergone some plastic deformation.
Consider a typical L-Clip. Mostly, the peak stresses will be in the bent/radius region of the clip. Lets say that the peak stress value is beyond Fty and the clip has some permanent strain in the bent region.
1. Has the stiffness (Modulus) softened in the circled region due to permanent strain?
2. If further loading is below DLL (say 0.75 of DLL) in the clip, how does the clip, especially the circled region behave? What would be the stress values in the above region?
Would like to get a better understanding of the physics.
How would be the behavior of a fitting/structure which has undergone some plastic deformation.
Consider a typical L-Clip. Mostly, the peak stresses will be in the bent/radius region of the clip. Lets say that the peak stress value is beyond Fty and the clip has some permanent strain in the bent region.
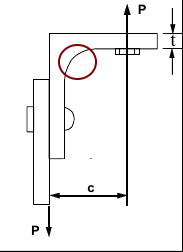
1. Has the stiffness (Modulus) softened in the circled region due to permanent strain?
2. If further loading is below DLL (say 0.75 of DLL) in the clip, how does the clip, especially the circled region behave? What would be the stress values in the above region?
Would like to get a better understanding of the physics.