Carreroal
Mechanical
- Jan 27, 2020
- 6
Hi everyone, I working in a injection chemical process for entrance of RO system, and the principal Pipe of feed system have 2600 mm of diameter. We have a proposal for material. We think in teflon for all the body of this injector with 30ª of inclination respect to the vetical.
Any of you have experience about materials and injectors for big diamenters? (1.8 m/s fluid velocity)
Thanks in advantage.
Regards
Ander
Any of you have experience about materials and injectors for big diamenters? (1.8 m/s fluid velocity)
Thanks in advantage.
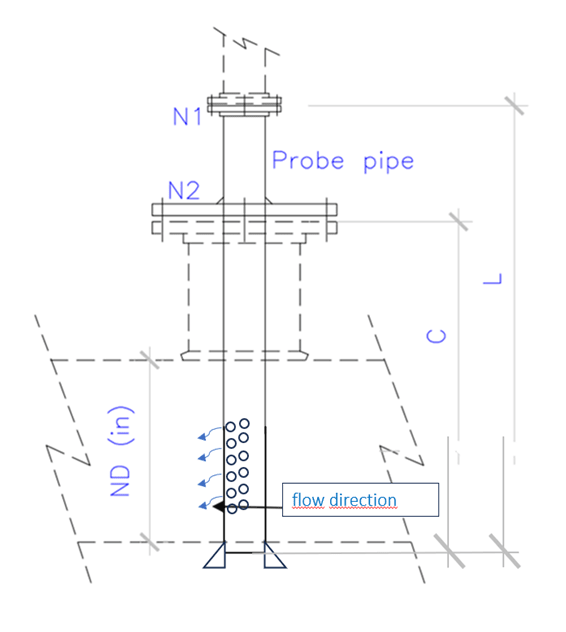
Regards
Ander