Hi all.
Please refer to the images below showing dimensions and a tolerance table for a relief geometry at the end of an internal or external thread.
I have two general questions:
1. What are some common measurement means to inspect these requirements (distances and angles with tolerances), on an outside (threaded shaft), and inside (threaded hole) areas of a mechanical component?
2. If the dimensions were changed to "basic dimensions" and the requirements were given as a profile of a surface geometric tolerance, would that force a change in the measurement methods, and would it make inspection easier or more difficult and costly, for the internal and external cases?
Thanks in advance.
Please refer to the images below showing dimensions and a tolerance table for a relief geometry at the end of an internal or external thread.
I have two general questions:
1. What are some common measurement means to inspect these requirements (distances and angles with tolerances), on an outside (threaded shaft), and inside (threaded hole) areas of a mechanical component?
2. If the dimensions were changed to "basic dimensions" and the requirements were given as a profile of a surface geometric tolerance, would that force a change in the measurement methods, and would it make inspection easier or more difficult and costly, for the internal and external cases?
Thanks in advance.
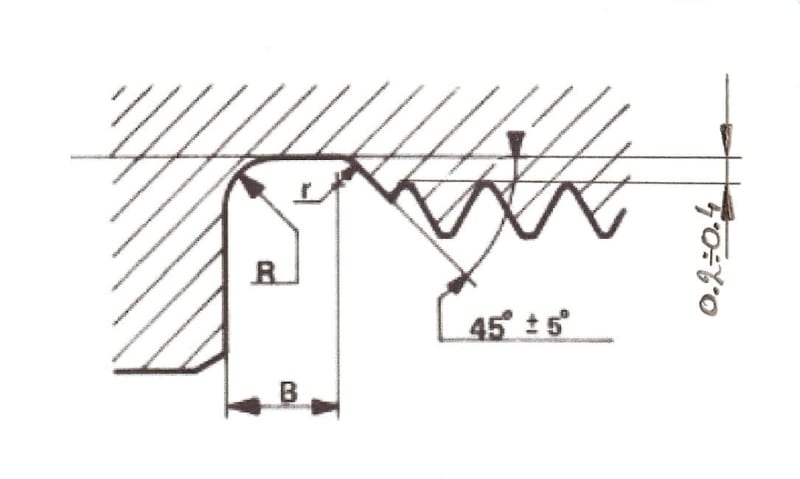
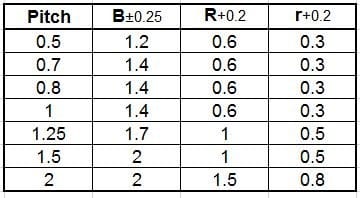