I don't have experience designing plastic parts that mate together, so I'd appreciate some pointers.
Basically I ordered plastic gas diffuser that will be pressed to fit, and I have made the inner diameter of the filter too loose, causing gas to leak from the mating surfaces.
Both diameters I have specified to be 10mm. In hindsight should have made diffuser ID smaller. Any general rule of thumb on interference fits on plastic parts - are they the same as on metals?
Basically I ordered plastic gas diffuser that will be pressed to fit, and I have made the inner diameter of the filter too loose, causing gas to leak from the mating surfaces.
Both diameters I have specified to be 10mm. In hindsight should have made diffuser ID smaller. Any general rule of thumb on interference fits on plastic parts - are they the same as on metals?
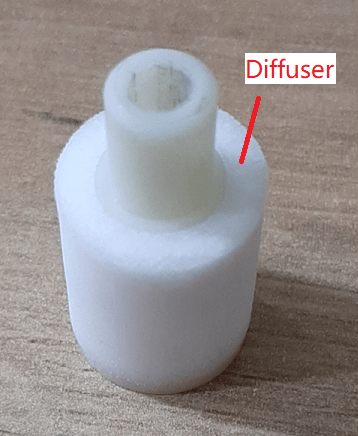