LL631
Industrial
- Nov 30, 2018
- 24
I have a small interference fit hub that I need to find the acceptable range of internal diameters for.
I've calculated that for loosest case (+0.007mm) a hub ID range of 8.5mm - 13mm should provide enough torque. However, due to machining tolerances on the shaft and hub the minimum tightest interference case possible is going to be approx. +0.025mm (.001"), at this interference I've found that for almost all diameters the equivalent stress due to interference pressure is beyond the tensile strength of the material. But this assumes that the hub is elastic. If the material is assumed to be perfectly plastic then increasing the interference (strain) beyond the point to cause yielding will not lead to an increased interface pressure, only further deformation of the hub? So the interface pressure can only increase to the point where it will cause yielding? Maybe..? I don't know..
Can anyone advise where I go with this? How I'd go about determining the integrity of the hub under such conditions?
I know changing the material / geometry could solve this problem but I am trying to analyse an existing design (which works) which was based off "+0.001" should be alright." I'm also reasonably confident in my calculations as I've got the same data from a Kisssoft simulation.
I've calculated that for loosest case (+0.007mm) a hub ID range of 8.5mm - 13mm should provide enough torque. However, due to machining tolerances on the shaft and hub the minimum tightest interference case possible is going to be approx. +0.025mm (.001"), at this interference I've found that for almost all diameters the equivalent stress due to interference pressure is beyond the tensile strength of the material. But this assumes that the hub is elastic. If the material is assumed to be perfectly plastic then increasing the interference (strain) beyond the point to cause yielding will not lead to an increased interface pressure, only further deformation of the hub? So the interface pressure can only increase to the point where it will cause yielding? Maybe..? I don't know..
Can anyone advise where I go with this? How I'd go about determining the integrity of the hub under such conditions?
I know changing the material / geometry could solve this problem but I am trying to analyse an existing design (which works) which was based off "+0.001" should be alright." I'm also reasonably confident in my calculations as I've got the same data from a Kisssoft simulation.
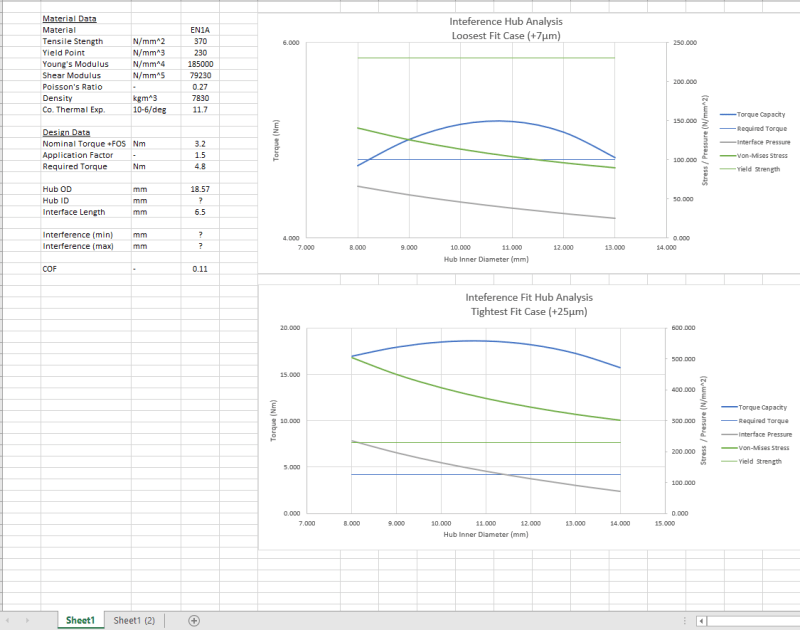