rollingcloud
Aerospace
- Aug 9, 2022
- 173
My main concern is the distance between the char 36 (Ø0.312 - Ø0.314) hole and the char 40 (Ø0.377 - Ø0.379) hole. This distance is not explicitly shown on the drawing, but it can be calculated in its basic form using char 49 and char 59 & 60, yielding 0.8133. My goal is to determine the smallest possible distance as a result of the FRTZF or how much that .8133 will be decreased by.
Since the FRTZF has a 0.007 diametrical tolerance zone and the distance between the holes in the Y-direction is not controlled by the FRTZF, only char 49 is directly affected by the 0.007 tolerance. In the worst-case scenario, the new distance between the holes would be: 0.8133 - 0.007 = 0.8063. Can someone confirm if my understanding is correct?
----------------------------------------------------------------------------------------------------------------------
(On a related note, I noticed some questionable aspects of this drawing. For example, is char 37 even valid? The PLTZF has a basic dimension for the Y-direction (char 59), but the X-direction is not defined using a basic dimension. Instead, it relies on dim Q, which has a tolerance relative to the edge (not a datum).
That said, I suppose it's still somewhat interpretable. Perhaps the intention was: "The hole location in the X-direction must first meet dim Q, and then its Y-location must conform to char 37." Essentially, this approach mixes hard dimensions with basic dimensions—though separately. Just not sure if its legal per Y14.5.)
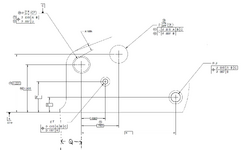
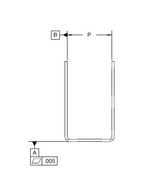
Since the FRTZF has a 0.007 diametrical tolerance zone and the distance between the holes in the Y-direction is not controlled by the FRTZF, only char 49 is directly affected by the 0.007 tolerance. In the worst-case scenario, the new distance between the holes would be: 0.8133 - 0.007 = 0.8063. Can someone confirm if my understanding is correct?
----------------------------------------------------------------------------------------------------------------------
(On a related note, I noticed some questionable aspects of this drawing. For example, is char 37 even valid? The PLTZF has a basic dimension for the Y-direction (char 59), but the X-direction is not defined using a basic dimension. Instead, it relies on dim Q, which has a tolerance relative to the edge (not a datum).
That said, I suppose it's still somewhat interpretable. Perhaps the intention was: "The hole location in the X-direction must first meet dim Q, and then its Y-location must conform to char 37." Essentially, this approach mixes hard dimensions with basic dimensions—though separately. Just not sure if its legal per Y14.5.)
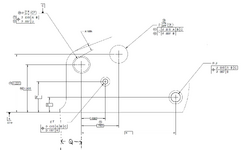
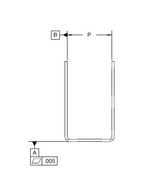