Is there a steel alloy that is stronger than 1018 and can be welded to A36 plate?
By stronger, I mean a higher tensile strength.
The material needs to be machined before welding.
The application is a shaft that a hub assembly with bearings bolts on to (similar to a weld-on trailer axle stub shaft).
By stronger, I mean a higher tensile strength.
The material needs to be machined before welding.
The application is a shaft that a hub assembly with bearings bolts on to (similar to a weld-on trailer axle stub shaft).
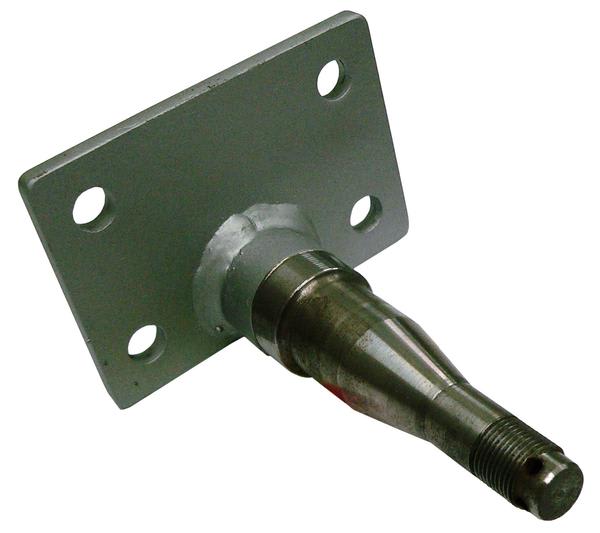