dexion7
Automotive
- Dec 8, 2010
- 26
I'm planning to make a mount to support a 150kg engine from a solid 200mm x 38 x 50 rectangular section aluminum bar of which each end will have an M16 hole tapped and fitted with a rose joint, the bores of which will be bolted to the chassis. obviously there would be a washer and then a lock nut securing each rose joint.
the centre point of the bar would take the engine weight (via a rubber mount) but the torque reaction of the engine would have a tendency to try and exploit any clearance between the rose joint threads and those of the tapped holes.
obviously a rose joint is designed to work in tension but in this case there will be a load which is effectively on the side of the threads.
is this still all a bad idea or, if its ok, would a coarse thread rose joint be better than a fine thread?
the centre point of the bar would take the engine weight (via a rubber mount) but the torque reaction of the engine would have a tendency to try and exploit any clearance between the rose joint threads and those of the tapped holes.
obviously a rose joint is designed to work in tension but in this case there will be a load which is effectively on the side of the threads.
is this still all a bad idea or, if its ok, would a coarse thread rose joint be better than a fine thread?
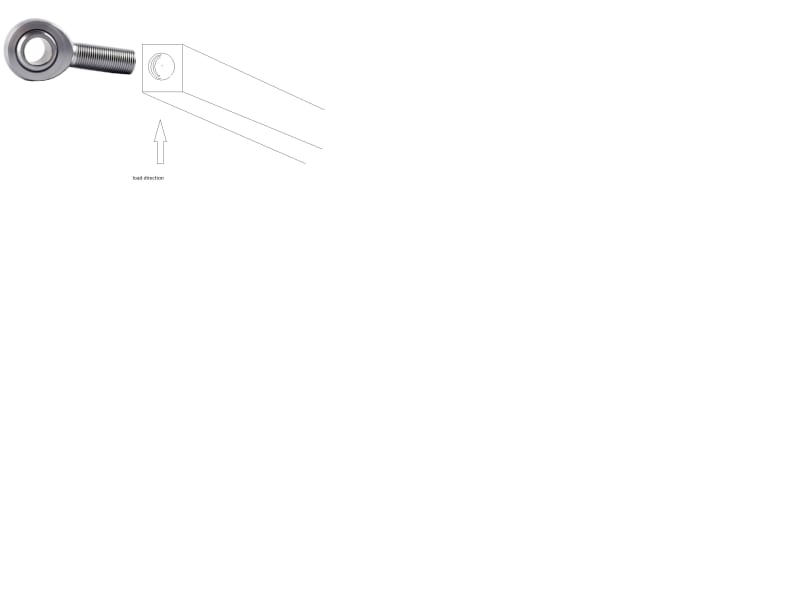