Dear All,
One of our plant motor has recently Burnt. It was newly installed and within 8-months even not being in continuous operation (Operating in duty cycle on/off).
Motor rating: 400Vac 50Hz 36A 18.5KW 1465rpm Cos phi 0.84
The operating conditions for this motor were same as of original existing motors that is balanced three phase power supply without any harmonics, no overloading (electrical or mechanical), ambient temperature less than mentioned on motor data sheet and name plate(+50°C).
Our Maintenance department has the following assessment:
1. Motor quality was not as the existing original motors.
2. The original motor Insulation class is F/F. While the burnt motor Insulation class is F/B. That is Insulation class F but limited to temperature rise of class B. (Motor data sheet).
3. The Type of newly supplied motor is D5C while the existing motor has type D4C. Same difference exists in their serial nos. (Manf. Confirmed motor is same but with new series).
4. The motor was supplied without any QA/QC, test certificates, performance curves, and conformities.
5. No factory acceptance test or third party inspection was made/involved.
6. Considering new motor from factory no tests were conducted by our maintenance department and motor was directly installed.
7. The RTDs in the motor were not connected to any PTC relay. As in original motor starter this option is not available. (Motor Starter Wiring Diagram).
8. The newly supplied motor had insulation failure specially the place of embedded RTDs. Two phase winding were shorted.
9. Protection system worked, the only short circuit by the MCCB found tripped and earth fault relay found tripped.
Could you please identify the true cause of stator winding flashover, and recommendation,
shall be highly appreciated.
Please feel free to ask any further details you may require.
Best Regards
One of our plant motor has recently Burnt. It was newly installed and within 8-months even not being in continuous operation (Operating in duty cycle on/off).
Motor rating: 400Vac 50Hz 36A 18.5KW 1465rpm Cos phi 0.84
The operating conditions for this motor were same as of original existing motors that is balanced three phase power supply without any harmonics, no overloading (electrical or mechanical), ambient temperature less than mentioned on motor data sheet and name plate(+50°C).
Our Maintenance department has the following assessment:
1. Motor quality was not as the existing original motors.
2. The original motor Insulation class is F/F. While the burnt motor Insulation class is F/B. That is Insulation class F but limited to temperature rise of class B. (Motor data sheet).
3. The Type of newly supplied motor is D5C while the existing motor has type D4C. Same difference exists in their serial nos. (Manf. Confirmed motor is same but with new series).
4. The motor was supplied without any QA/QC, test certificates, performance curves, and conformities.
5. No factory acceptance test or third party inspection was made/involved.
6. Considering new motor from factory no tests were conducted by our maintenance department and motor was directly installed.
7. The RTDs in the motor were not connected to any PTC relay. As in original motor starter this option is not available. (Motor Starter Wiring Diagram).
8. The newly supplied motor had insulation failure specially the place of embedded RTDs. Two phase winding were shorted.
9. Protection system worked, the only short circuit by the MCCB found tripped and earth fault relay found tripped.
Could you please identify the true cause of stator winding flashover, and recommendation,
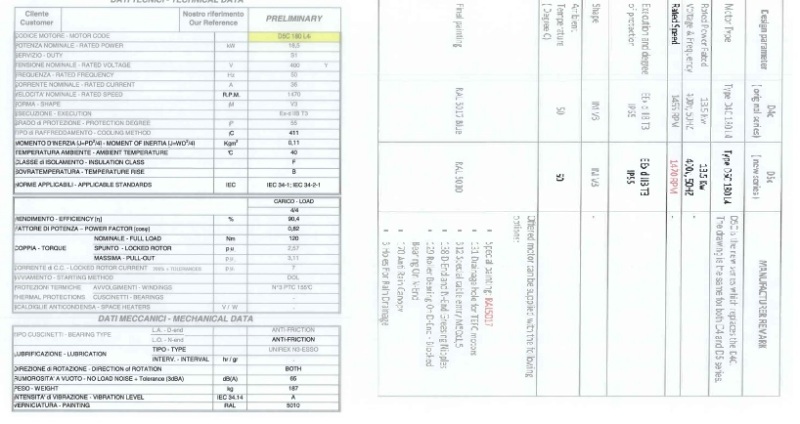
Please feel free to ask any further details you may require.
Best Regards
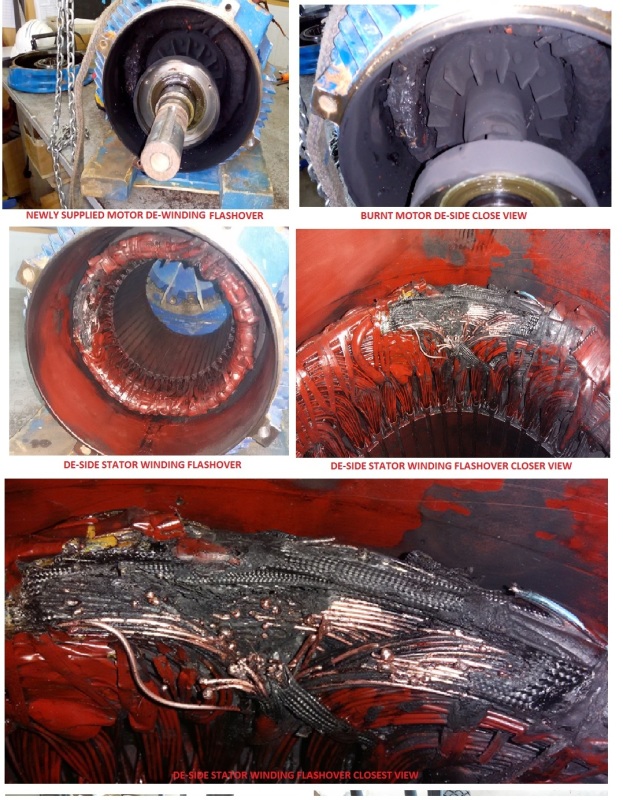
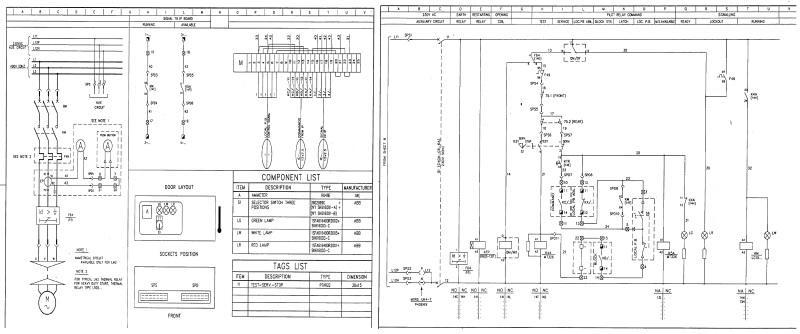
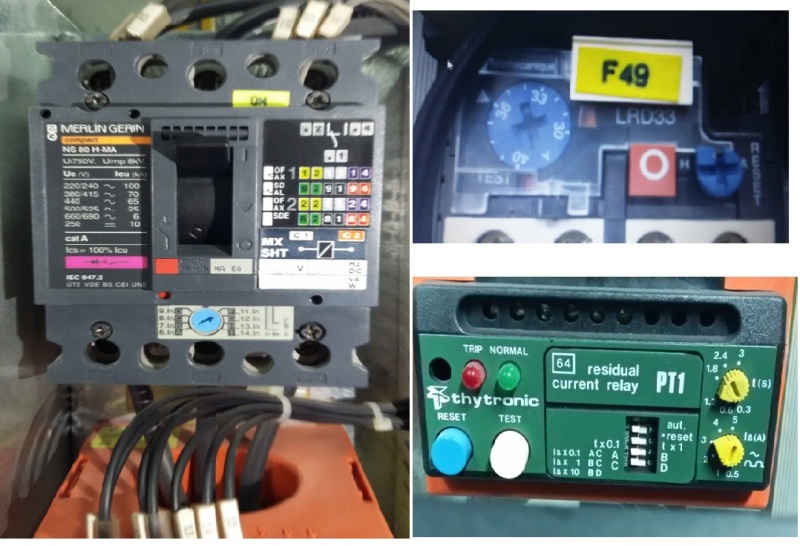