Jhinnie2
Structural
- Sep 28, 2021
- 9
Hi there,
Engineer here with no experience with real-world welding so if someone let me know if this will work that would be awesome. Essentially we have a column sitffener that will be fllet welded in place, and then a big thick bearing plate will need to contact the column, and also a large beam (that is also connected to the column). Just wondering is it possible to fillet weld or potentially butt weld from one side (top face) the column stiffener to the thick end plate, say if the the end plate extends vertically 10 or 20 mm? It's quite tight in space, the column is 6" x 8" (150 mm flange width x 205 mm depth. The coumns will be boxed out, so another vertical plate will be welded on top of this thick end plate - hopefully the screenshots make sense. Other option is to extend the stiffener across the top of the thick end plate, but this would put the weld under a lot of shear rather than bearing? Thanks
Engineer here with no experience with real-world welding so if someone let me know if this will work that would be awesome. Essentially we have a column sitffener that will be fllet welded in place, and then a big thick bearing plate will need to contact the column, and also a large beam (that is also connected to the column). Just wondering is it possible to fillet weld or potentially butt weld from one side (top face) the column stiffener to the thick end plate, say if the the end plate extends vertically 10 or 20 mm? It's quite tight in space, the column is 6" x 8" (150 mm flange width x 205 mm depth. The coumns will be boxed out, so another vertical plate will be welded on top of this thick end plate - hopefully the screenshots make sense. Other option is to extend the stiffener across the top of the thick end plate, but this would put the weld under a lot of shear rather than bearing? Thanks
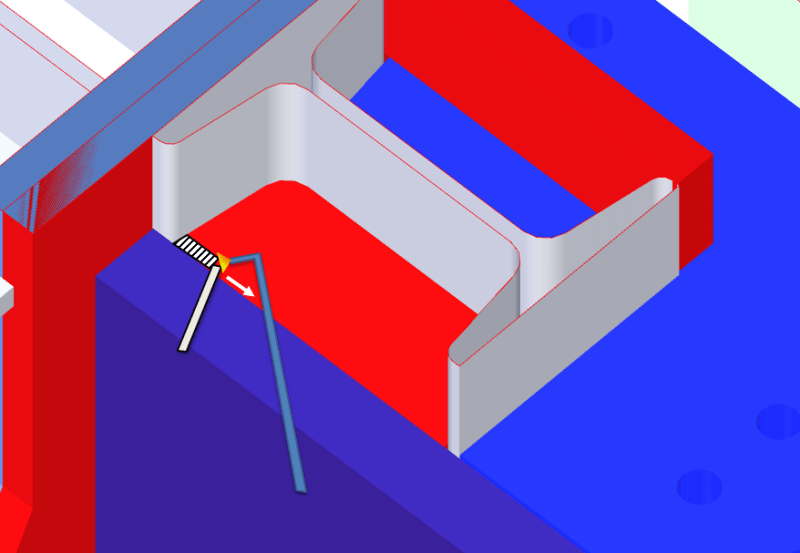
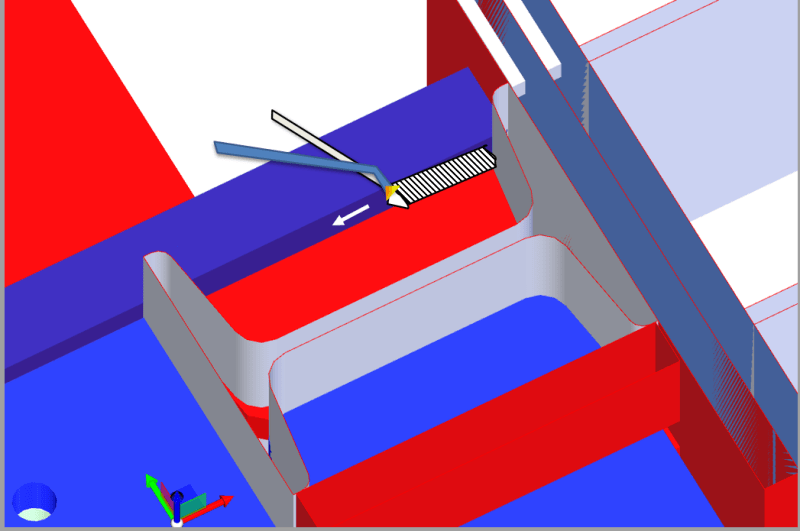
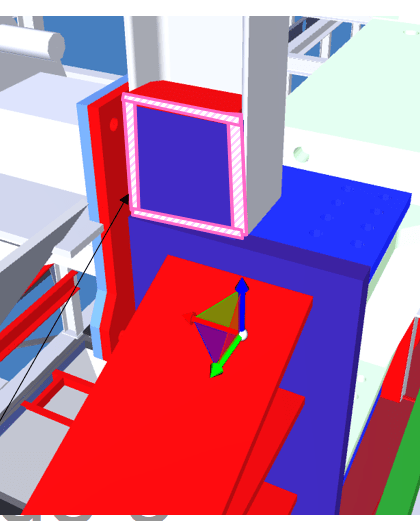