smokiibear
Structural
I provide engineering for light guage steel covers with Solar atop. They are light gauge purlins, light gauged metal roof. When columns reach over 14.75', I've typically followed the recommendation to not exceed Kl/r < 200, and consequently, forced to go to 6" std pipe. I'm curious if you could comment. I don't think it's warranted on these tiny structures, but don't want to make a poor choice. Could you comment.
Here is a sample of the product.
Here is a sample of the product.
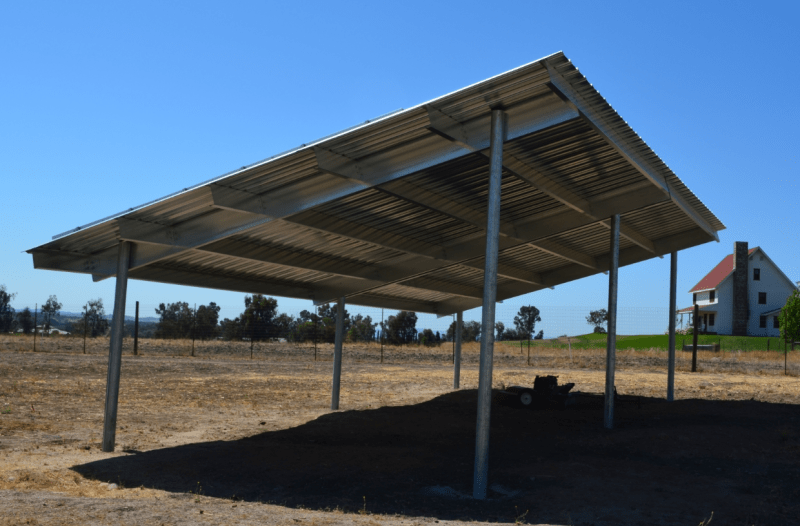