JanEngineer
Mechanical
I'm making a model for a pressure vessel. First i made one quickly with 3D solid mesh tetra10 noded. But because i wanted to make some adjustments it was easier to make a plate mesh. Locally the stress is larger for my plate mesh than my solid mesh and i don't understand why. Thicknesses are similar and displacement also.
Does anyone know how this could be? Is there something wrong with one of my models or is there a fundamental difference between the elements that causes this?
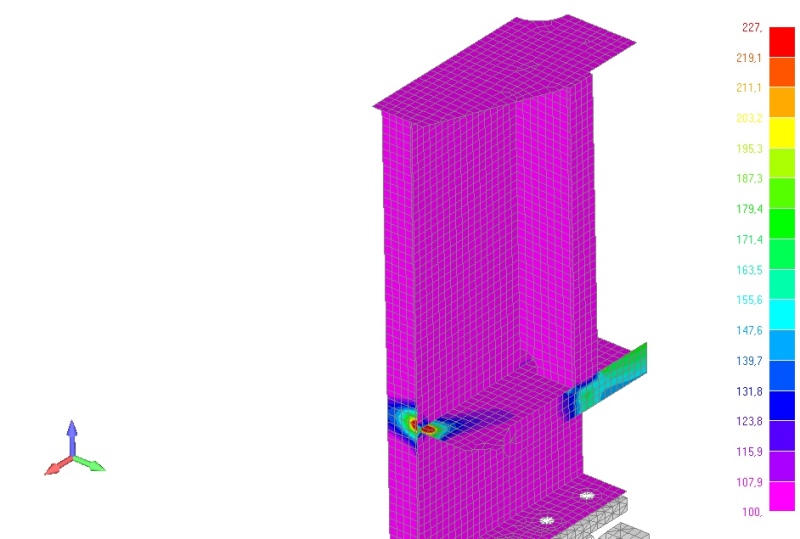
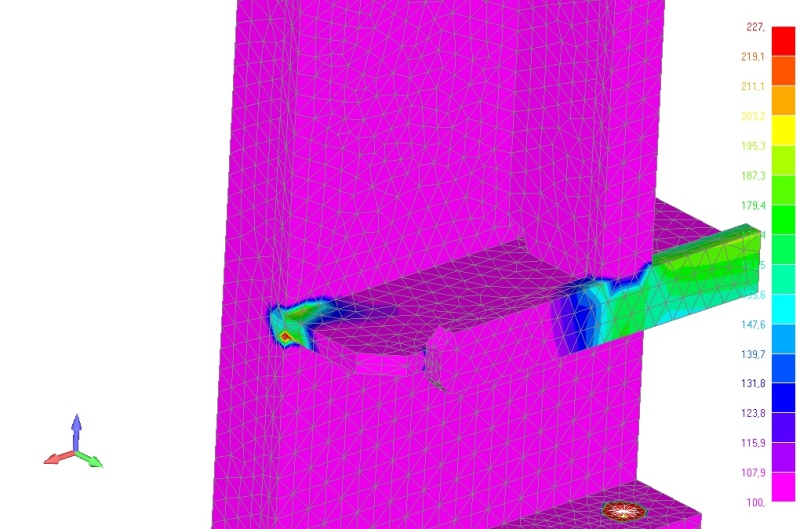
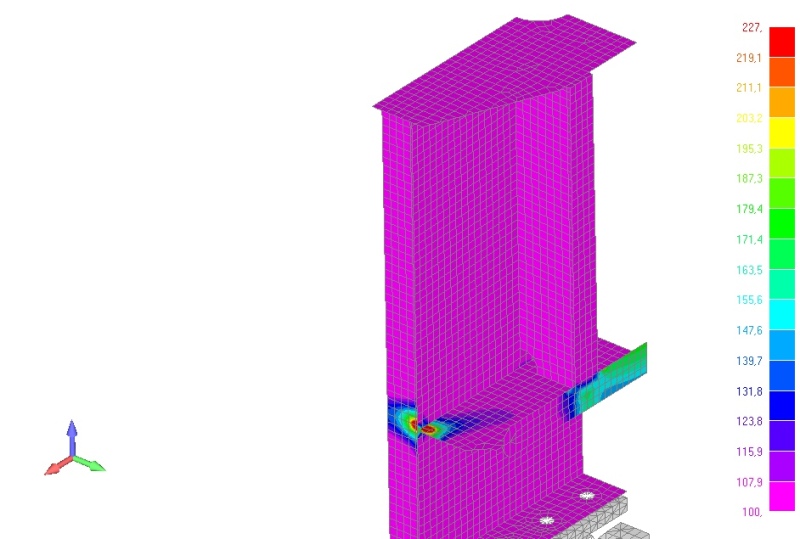
Does anyone know how this could be? Is there something wrong with one of my models or is there a fundamental difference between the elements that causes this?