TRAK.Structural
Structural
- Dec 27, 2023
- 306
Doing a residential screened porch addition and need some input on how others would approach the lateral design for this. Generally I wouldn't be too concerned here except this particular design does have a fair amount of wall area that will receive wind pressure, see plan below, wall on left side is solid, remainder is screened. N-S direction will go through the roof diaphragm and into the main house however the E-W loading (which has more wind area) probably needs some closer analysis.
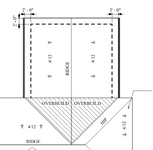
- How would you determine MWFRS pressures for the wall/roof? ASCE 7 open structures provisions?
- Would you try to make cantilevered posts work to resist wind loading, or some combination of cantilevered posts and new/existing walls accounting for geometry and stiffness of elements? Some other approach?
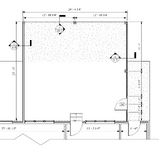
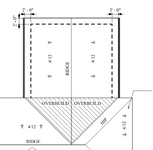