majkus
Mechanical
- Dec 7, 2018
- 5
Hello,
I am looking for lifting solution , I have a steel structure of weight - 2,6 tonne that needs to be lifted by H = 650mm with MANUAL actuation , if needed cordless drill is applicable as well.
Picture below ( dimensions in mm )
For now i have thought of landing gear jacks in each corner [1,2,3,4] however i couldn't find suitable stroke, 510mm is maximum.
After lifting of H , 2 people will be working on the top - surface ( 5 ). Surface 5 is inclined about 10 degrees horizontally. Assume that CoG is perfectly in between support 1,2,3,4 at 2000mm height.
I also thought of something central with retractable jack stands with some sort of ratchet ( green ) and central lifting with hydraulic piston (red) with a hand pump
See video below :
What other solutions or comments come to your mind?
I am looking for lifting solution , I have a steel structure of weight - 2,6 tonne that needs to be lifted by H = 650mm with MANUAL actuation , if needed cordless drill is applicable as well.
Picture below ( dimensions in mm )
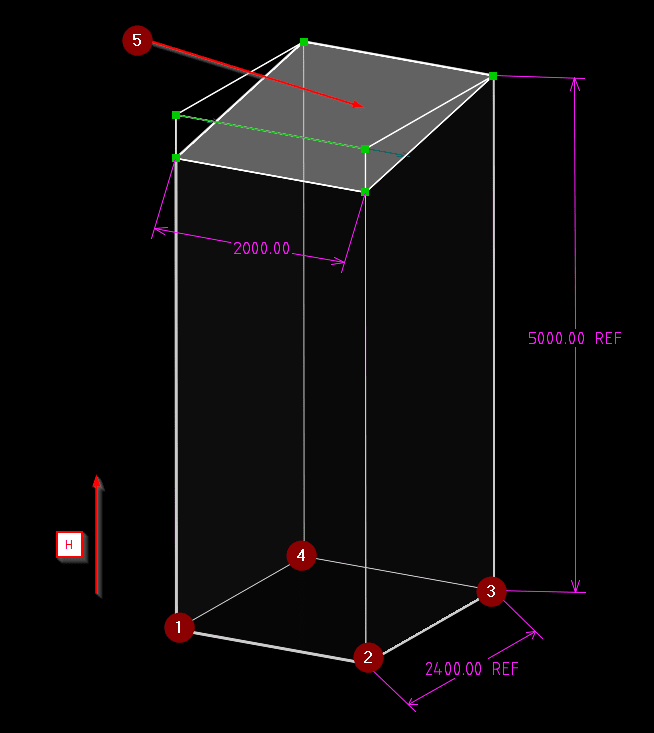
For now i have thought of landing gear jacks in each corner [1,2,3,4] however i couldn't find suitable stroke, 510mm is maximum.
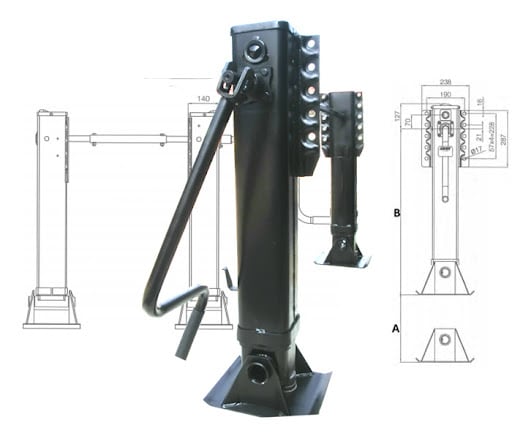
After lifting of H , 2 people will be working on the top - surface ( 5 ). Surface 5 is inclined about 10 degrees horizontally. Assume that CoG is perfectly in between support 1,2,3,4 at 2000mm height.
I also thought of something central with retractable jack stands with some sort of ratchet ( green ) and central lifting with hydraulic piston (red) with a hand pump
See video below :
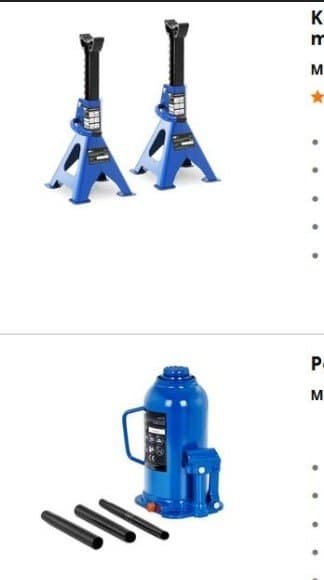
What other solutions or comments come to your mind?