julian89
Mechanical
- Nov 11, 2013
- 33
Hi all,
I have begun to look into performing FEAs in accordance with EN 1993-1-5, and was a bit puzzled by Annex C of this standard which provides the rules. It allows the engineer to use any material model from linear elastic up to full elastic plastic, but does not mention any load factors associated with these models. My background is largely in the world of pressure vessel, and in that world there are distinct load factors associated with the material models one uses (e.g. ASME VIII Div. 2 etc).
Simply put, from what I can read from Cl. C.9 of EN 1993-1-5, we can use any material model, but the load factors and material factors have to be taken into consideration (here it is referred to EN 1990 Annex D which is for testing and has a strong emphasis on statistical approaches etc.).
JRC has released a document titled "COMMENTARY AND WORKED EXAMPLES TO EN 1993-1-5 'PLATED STRUCTURAL ELEMENTS'" (this is readily available on the web), but also here the guidelines are pretty diffuse.
Has anyone here had experience using elastic-plastic FEAs and EN 1993-1-5? What load factors do we use when performing an elastic-plastic analysis?
I have begun to look into performing FEAs in accordance with EN 1993-1-5, and was a bit puzzled by Annex C of this standard which provides the rules. It allows the engineer to use any material model from linear elastic up to full elastic plastic, but does not mention any load factors associated with these models. My background is largely in the world of pressure vessel, and in that world there are distinct load factors associated with the material models one uses (e.g. ASME VIII Div. 2 etc).
Simply put, from what I can read from Cl. C.9 of EN 1993-1-5, we can use any material model, but the load factors and material factors have to be taken into consideration (here it is referred to EN 1990 Annex D which is for testing and has a strong emphasis on statistical approaches etc.).
JRC has released a document titled "COMMENTARY AND WORKED EXAMPLES TO EN 1993-1-5 'PLATED STRUCTURAL ELEMENTS'" (this is readily available on the web), but also here the guidelines are pretty diffuse.
Has anyone here had experience using elastic-plastic FEAs and EN 1993-1-5? What load factors do we use when performing an elastic-plastic analysis?
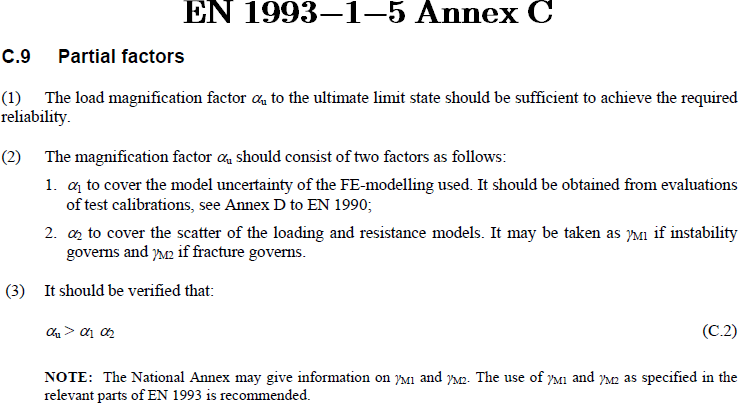
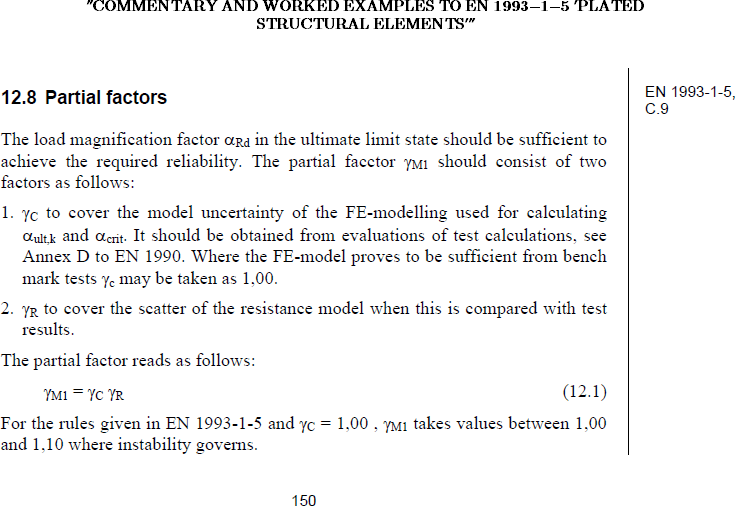