Designer80
Chemical
I have a question.
Recently one of our Low press Saturated steam ( 6.5 barg) mettalic expansion bellow got ruptured.when steam was isolated for few minutes (30 mins) and then again opened through crack opening the manual valve (shown in the sketch).A hammer sound appeared and bellow ( encircled in the sketch) got ruptured.We have checked any possibility of condy logging through reverse flow of condensate in the steam line which could have resulted hammering and consequently failing the bellow.
Can you please share your experience, what could have gone wrong and what precautions we can take in future?
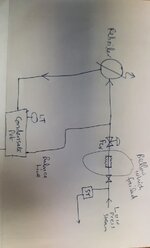
Recently one of our Low press Saturated steam ( 6.5 barg) mettalic expansion bellow got ruptured.when steam was isolated for few minutes (30 mins) and then again opened through crack opening the manual valve (shown in the sketch).A hammer sound appeared and bellow ( encircled in the sketch) got ruptured.We have checked any possibility of condy logging through reverse flow of condensate in the steam line which could have resulted hammering and consequently failing the bellow.
Can you please share your experience, what could have gone wrong and what precautions we can take in future?
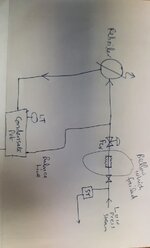